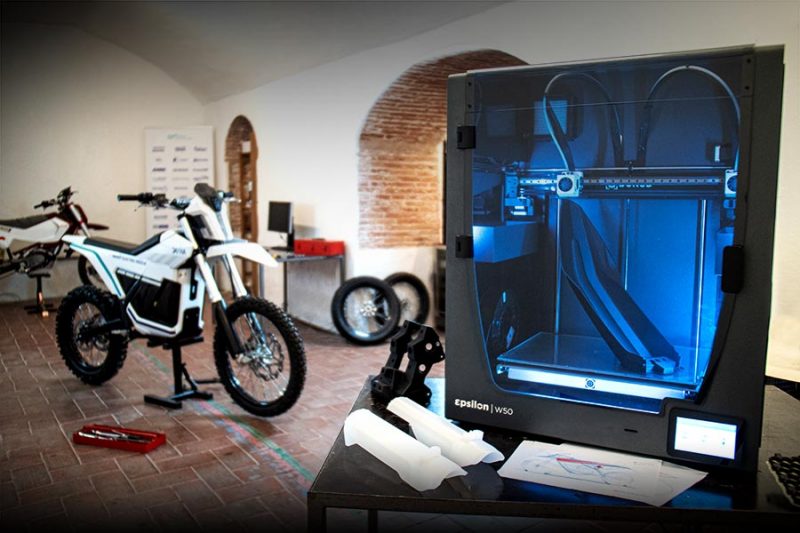
Nel settore automobilistico i processi di stampa 3D sono ormai entrati a pieno titolo tra quelli necessari non più solo nella progettazione e prototipazione, ma anche nella produzione vera e propria. Con la stampa 3D si realizzano molti componenti da integrare nei veicoli e si producono anche molti degli attrezzi utilizzati lungo le catene di produzione. Si possono poi risolvere anche problematiche di progettazione e produzione tipiche per componenti che sono fuori mercato o altrimenti inaccessibili per tempi o costi eccessivi.
Motocicletta per soccorso alpino
Una moto completamente elettrica per prestare primo soccorso in montagna, in grado quindi di muoversi su terreni difficili. Questo è il progetto che Elisava Racing Team, un gruppo di ingegneri del design industriale e studenti universitari di design di Barcellona stanno mettendo a punto in collaborazione con la società spagnola BCN3D, specializzata in produzione additiva. La motocicletta Dayna, dedicata esclusivamente al soccorso alpino, conta 19 parti finite stampate con tecnologia FFF (Fused Filament Fabrication), diverse per dimensioni e materiali utilizzati. La società specializzata nella stampa 3D ha permesso l’ottimizzazione del design e dei componenti, così da facilitarne la stampa, migliorare la qualità e ridurre i supporti altrimenti necessari durante la stampa. Sono stati scelti materiali rinforzati e non, con una notevole libertà di definizione della forma di ogni componente.
Trattandosi di elementi anche di grandi dimensioni, il team Elisava ha deciso di utilizzare la stampante 3D Epsilon W50 di BCN3D, la più grande della serie. Il grande volume di stampa di questo modello ha permesso di produrre anche parti come il parafango e il copri forcella. Per le parti a contatto con le batterie e l’elettronica, è stato scelto un filamento in ABS data la sua resistenza meccanica strutturale, resistenza termica e la carica statica bassa. La poliammide è stata utilizzata invece per le parti la cui resistenza all’abrasione e all’usura è essenziale. Per poter garantire le prestazioni meccaniche migliori in termini di resistenza alle severe condizioni di utilizzo della motocicletta, alcuni componenti sono stati realizzati con compositi con diverse percentuali di fibre, come la poliammide ad alta temperatura rinforzata con il 15% di fibra di carbonio (PAHT CB15). Il polipropilene caricato con 30% di fibra di vetro (PP GF30) è stato utilizzato invece per il parafango, poiché è uno dei componenti che rischia maggiormente rotture da urti e abrasioni. Questo materiale è infatti in grado di sopportare questo tipo di stress e tutte le sollecitazioni a cui la moto è sottoposta ed è inoltre più leggero del grado PAHT. Le proprietà di questi materiali, assieme all’ottimizzazione della resistenza alle forze di taglio durante il processo di stampa, hanno soddisfatto i severi requisiti strutturali necessari sia nella lavorazione sia nel componente finito.
La modalità Mirror della stampante Epsilon W50, tecnologia che consente la stampa simultanea di modelli specchiati in modo simmetrico, garantisce tempi di stampa rapidi, mentre il copolimero del butandiolo e dell’alcol vinilico BVOH ha garantito una iterazione rapida e una qualità elevata nella produzione di elementi dalla geometria complessa e meccanismi movibili. Una volta stampati, i pezzi sono stati sottoposti a levigatura, per conferire loro una finitura liscia.
Parti di ricambio per filobus
La società di ingegneria 3DnA focalizzata sulle tecnologie di additive manufacturing, con sede a Pomigliano D’Arco (NA), ha riprogettato e prodotto delle parti di ricambio per i filobus del servizio di trasporto pubblico ANM di Napoli.
La produzione di questi pezzi di ricambio è stata resa possibile dalla re-ingegnerizzazione e dalla stampa 3D di componenti meccanici non più disponibili nella catena di fornitura e di cui non è stato possibile recuperare la documentazione tecnica e i disegni originali.
Il filobus è collegato alle linee del cavo di alimentazione tramite un trolley head (il supporto della rotellina di presa) che prende la corrente e guida meccanicamente le aste fissate sui tetti del filobus.
I tempi di consegna di questo componente realizzato con metodi tradizionali avrebbe richiesto tempi di attesa fin anche di un anno, con conseguenti danni per il trasporto pubblico non potendo mettere in circolazione i mezzi con questi componenti obsolescenti. La scelta è quindi caduta sulla produzione additiva.
3DnA ha prima di tutto eseguito un processo di reverse engineering tramite scansione laser 3D per ricostruire le trolley head in un software di modellazione 3D. Una volta concordato su come dovessero essere i primi modelli, si è iniziata la stampa del prototipo.
Per le parti in alluminio è stato utilizzata la stampante 3D SLM 500 di SLM Solutions Group, che lavora su tecnologia additiva a fusione laser selettiva di polveri metalliche, mediante quattro laser a fibra ottica che si azionano contemporaneamente. Per le parti in plastica è stato utilizzato il sistema Fortus F900 FDM di Stratasys, con la resina Ultem 9085, termoplastica FDM ad alte prestazioni che consente ai produttori di creare prototipi funzionali e parti di produzione e che assicura un alto rapporto resistenza/peso, un’elevata resistenza termica e chimica e la conformità ai requisiti FST per fiamma, fumo e tossicità.
ANM ha poi testato i prototipi e, nel giugno 2020, sono stati inviati per l’approvazione all’Ufficio Trasporti Italiano. La produzione è poi iniziata e, ad oggi, due tipi di teste di carrello sono state riprogettate e prodotte in quantità.
La società di ingegneria di Pomigliano D’Arco ha già prodotto prototipi funzionanti per treni e droni con altre macchine Stratasys, ma ha potuto iniziare a soddisfare le richieste dei clienti per utensili e parti di produzione su larga scala, solo con l’introduzione nel suo impianto della stampante FDM F900. Con questa è possibile creare parti personalizzate fino a un metro di lunghezza a costi contenuti e accedere al contempo a una gamma più ampia di materiali ad alte prestazioni.
La F900 è infatti una stampante 3D per produzioni su larga scala dotata di un piatto di stampa con una dimensione di 914,4 x 609,6 x 914,4 mm, in grado di garantire precisione di stampa e ripetibilità elevate. Il sistema può stampare in 14 materiali termoplastici ad alte prestazioni, tra cui ABS, policarbonato, poliammide 12 caricata con fibre di carbonio, Antero 800NA (polimero PEKK) e resine Ultem 9085 e 1010.
Auto da corsa
Diverse sono le auto da corsa in cui si fa uso di parti realizzate con stampa 3D. Si va dai prototipi ai pezzi finali.
Williams Racing e la società californiana Nexa3D, specializzata in produzione additiva, hanno siglato una partnership che porta la stampa 3D rapida di polimeri nelle corse di Formula Uno.
La stampante 3D fotoplastica ultraveloce NXE400 di Nexa3D consente la produzione di parti funzionali della galleria del vento per i test aerodinamici. La velocità di produzione consente alla Williams di iterare e testare le parti più velocemente e di realizzare elementi leggeri ma sempre ad alte prestazioni.
Con questa tecnologia, Williams può infatti progettare e produrre rapidamente parti complesse e leggere in pochi minuti, riducendo al minimo l’utilizzo di materiale e gli sprechi, come alcuni elementi dell’auto e componenti della galleria del vento. Questo è possibile grazie a una velocità di stampa 20X con la tecnologia di fotopolimerizzazione del substrato lubrificante (LSPc) di Nexa e una matrice di luce strutturata in grado di raggiungere velocità massime di 1Z centimetro al minuto. Nel caso specifico si utilizzano materiali dedicati come il grado xGPP-Gray (General Purpose), una resina che assicura precisione nei dettagli e nelle finiture, e xCE-Black, una resina di estere di cianato ad alte prestazioni caratterizzate da proprietà isotrope elevate e notevole resistenza alla flessione.
Anche per la scuderia AlphaTauri uno degli elementi vincenti nella F1 è la stampa 3D e in questo caso con materiali DSM Somos (ora Covestro). La scuderia AlphaTauri utilizza infatti la produzione additiva per realizzare parti per i suoi modelli in galleria del vento. In particolare viene utilizzato il materiale Somos PerFORM Reflect per ridurre i tempi di produzione fino al 30%, migliorare le fasi di test e aumentare la velocità e la frequenza delle ottimizzazioni aerodinamiche.
Il team esegue test aerodinamici con un modello di galleria del vento e Computational Fluid Dynamics (CFD). Per aiutare a capire il flusso d’aria, viene utilizzata la velocimetria di imaging delle particelle (PIV). Telecamere ad alta velocità e un foglio di luce laser permettono di fotografare milioni di particelle trasportate nell’aria in tempi molto brevi. Queste immagini vengono analizzate per studiare l’aspetto dei campi del flusso d’aria intorno al veicolo e permettono così di intervenire per migliorare il design aerodinamico secondo le prestazioni necessarie in gara.
Di colore arancione, il materiale Somos PerFORM Reflect per stereolitografia ha una bassa viscosità e un basso assestamento per la produzione di parti rigide e resistenti alle alte temperature, ideali per modelli in galleria del vento e test PIV. Si possono realizzare anche parti complesse e particolarmente dettagliate in tempi rapidi e gli interventi di post-produzione sono ridotti al minimo, poiché non è necessario verniciare le parti. La composizione del materiale, tra l’altro, riduce al minimo il riflesso del foglio di luce laser, aumentando la qualità dei risultati PIV.
Un altro esempio di produzione additiva nel settore automobilistico arriva dalla Chevrolet Racing (gruppo GM) che ha già la tradizione di usare la stampa 3D, risultando efficiente, competitiva e produttiva.
I team di corse dell’azienda includono Nascar, le competizioni dell’International Motor Sports Association, le gare di resistenza del Grand Touring, le gare Indycar e altri eventi nordamericani. Le auto che Chevrolet schiera in questi eventi includono tutte componenti stampati in 3D, parti che condividono design e funzionalità con i veicoli standard di General Motors. Il 75% delle parti utilizzate per prototipare la Corvette 2020 di Chevrolet, ad esempio, sono state stampate in 3D.
Chevrolet ha una lunga storia di trasferimento tecnologico tra i team di corse e di produzione. La capacità di stampa 3D di General Motors accelera i cicli di apprendimento e, a sua volta, queste esperienze sui circuiti aiutano il team di produzione additiva a fare un passo avanti verso l’utilizzo di parti stampate in 3D nei veicoli di produzione.
Due nuove Corvette a motore centrale hanno debuttato nel gennaio 2020. Entrambe sono dotate di 75 parti stampate in 3D, tra cui il serbatoio dell’olio, l’ingresso e il tappo del serbatoio, la scatola di raffreddamento dell’aria condizionata del conducente e il sistema di idratazione integrato, la staffa della pompa del servosterzo e gruppi ottici. Cinquanta di queste parti sono state progettate o stampate internamente da GM.
Anche il programma Indycar ha avuto un grande successo sfruttando la stampa 3D per la Chevrolet Indy V6. I componenti del sistema di scarico Chevrolet Indycar V6 sono stampati in 3D, il che aiuta a eliminare i punti di guasto nei componenti fabbricati tradizionalmente, aumentando al contempo la libertà di progettazione e riducendo i costi. Il camion da corsa fuoristrada Silverado ha invece tre parti stampate in 3D realizzate internamente da GM, incluso un carter di protezione del sistema ammortizzatore posteriore realizzato con plastica rinforzata con fibra di carbonio, che protegge gli ammortizzatori posteriori dal terreno roccioso del deserto.
Chevrolet ha anche lanciato la Camaro ZL1 1LE per la Nascar Cup Series 2020. Le prestazioni aerodinamiche sono state ottimizzate attraverso test approfonditi e su vasta scala nella galleria del vento. Oltre 500 parti prototipo stampate in 3D sono state utilizzate nei test per sviluppare il nuovo corpo ZL1 1LE. Inoltre, questo modello è dotato di un condotto di raffreddamento dell’ingranaggio stampato in 3D.
Efficienza della produzione, consolidamento delle parti, creatività e risparmio sui costi sono alcune delle caratteristiche di cui Chevrolet Motorsports può avvantaggiarsi combinando ingegneria dei materiali, progettazione e produzione additiva.
Il veicolo “camaleonte”
L’azienda britannica Scaled Ltd, specializzata nella stampa 3D di grande formato tramite un processo di estrusione robotica, ha realizzato un veicolo elettrico stampato in 3D, il Chameleon. L’intenzione era di mostrare come il modo in cui i veicoli vengono prodotti può essere rivoluzionato attraverso la produzione additiva. Nella stampa 3D del telaio sono state utilizzate termoplastiche Lehvoss ad alte prestazioni con contenuto in plastica riciclata. I progettisti hanno anche utilizzato tecniche di progettazione emergenti come l’ottimizzazione con la topologia stocastica per rimuovere il materiale in eccesso e hanno voluto realizzare l’intero veicolo su una singola cella di produzione, denominata appunto Project Chameleon.
Il software utilizzato da Scaled è stato sviluppato dalla società Rafinex. Questo software lo si definisce stocastico, in quanto testa molte variazioni casuali nelle condizioni di carico prima di fornire un progetto strutturale ottimizzato finale. Questo processo garantisce che il design sia robusto, più adatto alle condizioni del mondo reale in cui impatti e carichi non avvengono mai come pianificato.
La piattaforma Project Chameleon è una cella di produzione che utilizza lo stesso hardware e software per la produzione di diversi tipi di veicoli, ovvero il cliente specifica le proprie esigenze e riceve un veicolo progettato per soddisfare in modo efficiente il proprio compito. Il veicolo in scala dimostra che il gioco cambia quando si porta la stampa 3D a questo livello: le parti possono essere rese anche più grandi, più robuste e più veloci. Il costo dell’intero veicolo è inferiore al costo di un singolo pannello di carrozzeria su alcuni veicoli. Si potrebbe così in futuro passare alla personalizzazione di massa. Questo cambio di paradigma è possibile grazie alla possibilità di prototipare e produrre utilizzando la stessa tecnologia: la stampa 3D su larga scala.
a cura di Valeria Mazzucato
Condividi l'articolo
Scegli su quale Social Network vuoi condividere