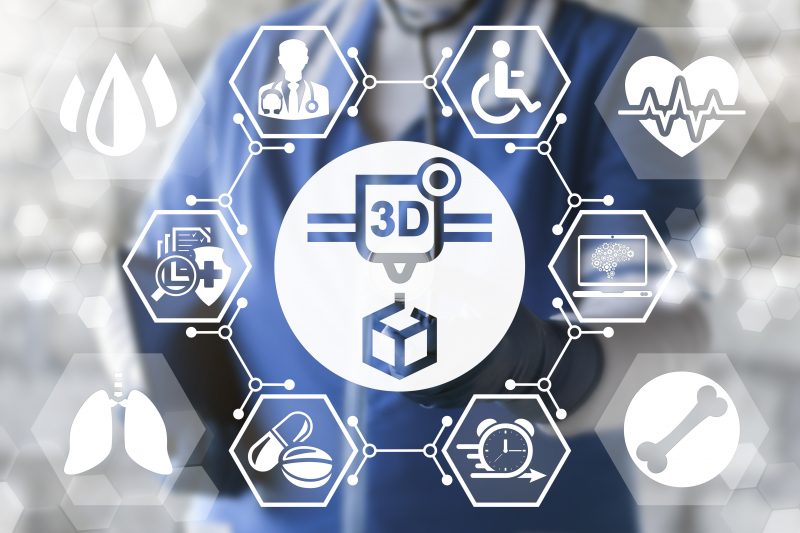
La sanità del futuro tra polimeri funzionalizzati e cliniche ospedaliere evolute in siti produttivi. Nuovi scenari grazie alla stampa 3D e alla formulazione di compound polimerici specializzati, unendo competenze ingegneristiche, chimiche e biomediche.
Il rapporto tra sanità e industria, negli ultimi tempi, è divenuto sempre più stretto, sia in termini di potenziamento della collaborazione tecnico-scientifica che di condivisione di scenari alternativi al classico rapporto committente-fornitore. Si stanno registrando, infatti, frequenti connessioni tra material scientist/fablab/technology provider per forniture dirette di materiali, in particolar modo polimerici, che possano rispondere a requisiti prestazionali utili nelle applicazioni più svariate che vanno, ad esempio, dalle protesi esterne, agli esoscheletri fino ad arrivare alla nuova frontiera della medicina rigenerativa e dell’ingegneria dei tessuti che mirano a riparare, rigenerare e riprodurre tessuti e organi danneggiati.
La possibilità di affrontare queste produzioni in un’ottica di medicina a misura del paziente grazie all’avvento della stampa 3D, inoltre, candida la clinica ospedaliera ad essere anche il sito di produzione di manufatti personalizzati per la specifica applicazione. È noto, infatti, che partendo dalle radiografie o dalle TAC dei pazienti è possibile convertire tali referti in dati di input per macchine di stampa 3D, le quali alimentate da un opportuno polimero sono in grado di riprodurre tridimensionalmente l’oggetto. A questo punto è la stessa clinica ospedaliera ad aver bisogno di materiale consumabile per le sue stampanti 3D, necessitando di polimeri con particolari funzionalità che potranno essere forniti come micro-produzioni da aziende specializzate. Lo scenario è quindi delineato. I professionisti della sanità saranno sempre più incentivati ad avvalersi di personale altamente qualificato nella Scienza dei Polimeri e di Equipment su scala di laboratorio che, vista la dimensione media delle produzioni (lotti da massimo 500g), potrebbe portare alcuni reparti ospedalieri a configurarsi come “sito produttivo qualificato”.
Polimeri e processabilità
I polimeri che si possono candidare come materia prima per processi di stampa 3D di manufatti realizzati direttamente in clinica possono suddividersi in due macrocategorie, a seconda che si tratti di prodotti che devono riassorbirsi nel corpo umano oppure rimanere durevoli.
Esistono infatti polimeri termoplastici cosiddetti bioriassorbibili, i quali hanno proprietà di biodegradazione specifica all’ambiente in cui possono essere impiantati, e polimeri termoplastici biocompatibili che possono invece resistere anche in ambienti severi come possono essere quelli a contatto con il plasma sanguigno senza comunque degradarsi. Tutti questi polimeri termoplastici a loro volta, grazie alla tecnologia del melt compounding, cioè l’additivazione in fuso polimerico, possono essere funzionalizzati per ottenere caratteristiche di antimicrobicità, radiopacità, elettroconduttività, termoconduttività, stimolazione della crescita cellulare. Estrusori di piccole dimensioni che mimano in tutto e per tutto estrusori industriali, collocati anche in laboratorio, sono in grado di produrre piccoli lotti di compound polimerici termoplastici dotati di tali caratteristiche.
Alcuni esempi di polimeri termoplastici biocompatibili e bioriassorbibili utilizzabili anche in estrusione e quindi compounding possono essere il Policaprolattone (PCL), il PLA (acido polilattico), PLG (copolimero di lattide e acido glicolico), PDS (Polidiossanone).
Tra i polimeri biocompatibili permanenti possiamo invece annoverare il TPU (Poliuretano termoplastico), il PE (Polietilene prodotto a varie densità), il PC (Policarbonato), il PMMA (Polimetilmetacrilato).
Polimeri con filler ad attività biologica/elettroconduttivi/radioopachi
Perché la cura medica possa essere sempre di più paziente specifica, la stampa 3D insieme alla possibilità di generare materiali polimerici tailor made, ovvero customizzati su requisiti specifici, sono un’ottima risposta. In particolare, il focus è nella produzione di granuli e filamenti calibrati di compound polimerici con proprietà quali l’antimicrobicità, l’elettroconduttività, la radiopacità o l’osteoconduzione. L’esperienza necessaria riguarda l’utilizzo all’interno delle matrici polimeriche di additivi con proprietà antimicrobiche a largo spettro piuttosto che specifici verso alcuni ceppi batterici o la capacità di realizzare polimeri additivati con antibiotici e antiinfiammatori che mantengono la loro efficacia anche dopo estrusione a temperature intorno ai 250°C.
Altri filler bioattivi sono il grafene ossido, utile sia come materiale in grado di generare elettroconduzione ma anche come materiale in grado di conferire proprietà di differenziazione cellulare piuttosto che di agevolazione alla crescita cellulare. Un altro settore di estremo interesse è quello dei materiali osteconduttivi mediante sviluppo di compound polimerici in polimero bioriassorbibile caricato con idrossipatite.
Vista infine la possibilità di realizzare in stampa 3D protesi permanenti con materiale polimerico e sapendo che tutti i polimeri termoplastici sono trasparenti ai raggi X, risulta di estremo interesse renderli radiopachi per monitorare le protesi all’interno dell’organismo dei pazienti. Il conferimento della radiopacità in polimeri termoplastici è possibile grazie alla scelta di opportuni filler radiopacizzanti che è possibile miscelare finemente e omogeneamente nella matrice polimerica con la tecnologia del melt compounding.
Additive manufacturing
Le stampanti 3D maggiormente presenti nella clinica medica sono quelle basate sulla tecnologia a filamento definite FDM (Fused Deposition Modeling) o le macchine da Bioprinting che invece lavorano con piccole cartucce di polimero in forma di granulo.
Entrambe le macchine possono lavorare finanche in ambiente sterile, possono perciò consentire la produzione di manufatti impiantabili per scopi di ricerca ma anche per cura clinica. Le stampanti possono lavorare con filamenti polimerici con diametri calibrati che vanno da 1,75 a 2,85 mm oppure con granuli polimerici. Il materiale polimerico utilizzato può essere un polimero termoplastico puro piuttosto che additivato con filler a funzionalità specifica.
Test e controllo qualità
I materiali polimerici a funzionalità specifica, sviluppati e prodotti in Nadir Plasma & Polymers, vengono caratterizzati al fine di conferire oltre al materiale anche una scheda tecnica che quantifichi le performance ottenute. In particolare, grazie ad una fitta rete di collaborazioni universitarie che vanno dall’Università Cà Foscari fino all’Università di Pisa, partner accademici di lunga durata, è in grado di offrire studi di microscopia e di diffrazione a raggi X che servono a fornire la morfologia del compound polimerico, piuttosto che studi di bioattività come la capacità antimicrobica di un particolare compound termoplastico. Anche proprietà di elettroconduzione e di resistenza termica vengono spesso caratterizzate nei compound generati.
Servizi e applicazioni industriali
Grazie a materiali polimerici come quelli fin qui descritti sarà possibile produrre dispositivi medici extracorporei con funzionalità antimicrobiche o elettroconduttive integrate piuttosto che oggetti impiantabili con capacità di rigenerazione ossea o di supporto nella fase post chirurgica. Molti materiali potranno anche essere utilizzati nella realizzazione di dispositivi medici wearable che possono essere utili nella diagnosi e monitoraggio di pazienti da remoto.
Chiaramente, mai come ora, è molto attuale la possibilità di generare materiali polimerici con capacità antimicrobica o persino antivirale che aiutino nella non proliferazione di microorganismi patogeni. Con tali materiali sarà possibile produrre sia componenti e arredi presenti nelle strutture ospedaliere piuttosto che dispositivi medici di largo consumo o superfici polimeriche.
Verso nuovi scenari
In uno scenario futuro è logico pensare che le competenze polimeriche e biomedicali possano integrarsi per arrivare a realizzare parti in grado di sostituire tessuti e organi danneggiati da traumi o malattie. Su questo argomento il Bioprinting e i materiali polimerici utilizzabili nelle macchine da Bioprinting permetteranno di realizzare organi più semplici come strutture cartilaginee delle orecchie o della trachea, dove la biostampa 3D utilizza degli “scaffold” disegnati in CAD e stampati in 3D usando materiali biocompatibili, sui quali verranno poi impiantate le cellule che formeranno i tessuti e l’organo, fino ad organi più̀ complessi e formati da moltissime cellule diverse, come il fegato, il cuore o i reni.
Il presente articolo è il risultato di un confronto tecnico e visionario con Marco Scatto, polymer scientist, con il quale sono stati analizzati alcuni scenari presenti e futuri dei materiali polimerici nel settore medicale. Lo sviluppo e la produzione di granuli e filamenti calibrati di compound polimerici, così come l’analisi e la valutazione di processi e nuove applicazioni possono essere approfonditi con Scatto mediante il sito: www.marcoscatto.com e mediante il sito www.nadir-tech.it.
Marco Scatto
Marco Scatto, Chimico Industriale specializzato in Scienza dei Polimeri. È autore di almeno 20 pubblicazioni scientifiche su riviste internazionali, autore di 4 brevetti.
Ad oggi è polymer scientist presso la Nadir S.r.l. e consulente nell’industrializzazione di prodotti e processi che riguardano le materie plastiche in svariati settori, dal biomedicale al packaging. Relatore in svariati congressi scientifici internazionali. Figura tra 50 esperti di Additive Manufacturing nominati dalla Commissione Europea.
Tra le altre attività è anche Consulente Senior in scrittura di proposte progettuali cofinanziate e Docente Esperto di Polimeri presso Istituto Italiano Imballaggio e altre società di formazione
Dal 2018 è Docente a contratto in Master Universitario di Specializzazione presso l’Università di Padova (Course in Packaging Materials Industry Specific courses (ISC 2) – Environmental Management and Regulatory Affairs in Fragrance and Cosmetics all’interno del Master in Business and Management (MBM) – Industry specific fragrance and cosmetic sector.
a cura di Ubaldo Spina
Condividi l'articolo
Scegli su quale Social Network vuoi condividere