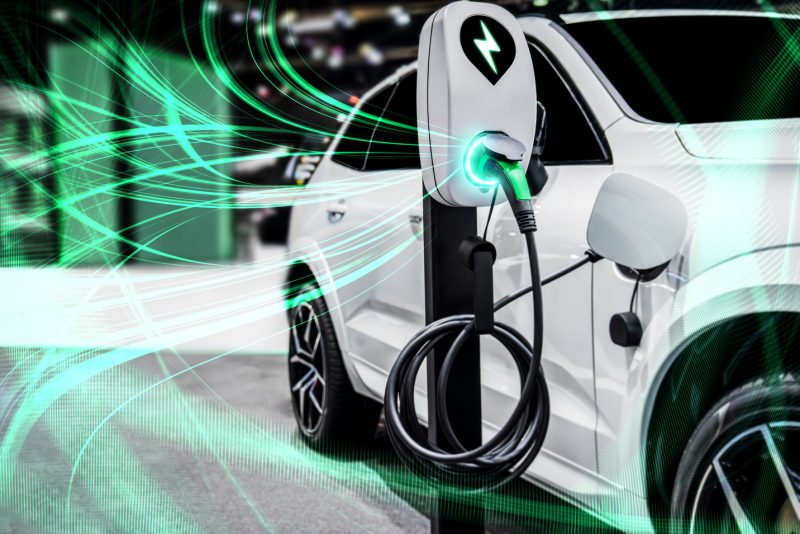
Il mercato automobilistico cinese ha gradualmente ripreso slancio nel 2023, mentre le prestazioni dei veicoli a nuova energia (NEV) si fanno sempre più interessanti. Alla luce dell’attuale tendenza del settore verso le joint venture “inverse” e l’export tecnologico, quali saranno i materiali plastici e le tecnologie di lavorazione necessari al settore NEV per offrire un’esperienza di guida più sicura, confortevole e sostenibile?
Secondo i dati diffusi dalla China Association of Automobile Manufacturers (CAAM), nei primi dieci mesi del 2023 la produzione e la vendita di automobili in Cina sono aumentate rispettivamente dell’8% e del 9,1% su base annua. Nel segmento dei NEV, la produzione e la vendita sono aumentate del 33,9% e del 37,8% nel periodo, consentendo a questi veicoli di raggiungere una quota di mercato pari al 30,4% del totale. Inoltre, le esportazioni di NEV hanno toccato le 995.000 unità, con una crescita del 99,1% rispetto al 2022.
La griglia, l’illuminazione e la ricarica evidenziano una tendenza verso la IA
I giovani consumatori rappresentano la fascia di età più attratta dai NEV. Importanti ricerche di mercato dimostrano che i consumatori di età inferiore ai 30 anni rappresentano il 43% circa degli utilizzatori di NEV. Inoltre, i giovani preferiscono i NEV di alto appeal estetico.
Come “volto” delle automobili di nuova generazione, le griglie con IA integrata diventano predominante in un segmento in cui anche i progressi nella tecnologia di stampaggio a iniezione e nei nuovi materiali svolgono un ruolo importante.
Tra gli esempi più rappresentativi vi è la griglia a forma di rene della BMW serie iX, che adotta la tecnologia di stampaggio integrato ideata da Engel per conferire un effetto 3D, o la griglia di Magna con IA integrata, che utilizza pannelli Mezzo in policarbonato per ottenere un effetto visivo altamente traslucido. Senza dimenticare Hyundai Mobis, che utilizza un’avanzata pellicola per lenti per rendere più sottile e leggero il modulo di illuminazione nella griglia.
Oltre alla griglia intelligente, le case automobilistiche hanno introdotto nuove idee per l’illuminazione supportate dall’IA e da tecnologie di lavorazione e materiali innovativi.
Ad esempio, i fari della BYD Yangwang U8 di sono prodotti sulla pressa a iniezione Tederic NEO M27220 che consente la realizzazione di parti di alta precisione, mentre le fanalerie del modello Li Auto L9 sono prodotte su grandi presse multicolore. Dal canto suo, HiPhi utilizza le soluzioni in policarbonato di Covestro per i fari e le griglie LiDAR del suo ultimo SUV di lusso. Inoltre, il PMMA multicolore di Wanhua Chemical aggiunge colore ai fanali posteriori intelligenti senza l’uso di vernici o spray, riducendo così le emissioni di carbonio.
Con la rapida evoluzione delle automobili che si servono dell’IA, anche i connettori per la ricarica dell’auto diventano più attraenti e facili da usare, offrendo agli utenti una migliore esperienza nella ricarica dei veicoli.
Ad esempio, lo sportellino del connettore della serie Audi e-tron completamente elettrica è realizzato in poliammide Akroloy PA GF 60 nera (6418) rinforzata con le fibre fornite da Akro-Plastic. WM Motor invece utilizza per questo stesso componente un compound PPE+PA leggero e sicuro, mentre Röchling ha presentato un rivestimento in biopolimero.
Le innovazioni di alleggerimento aumentano l’autonomia dei veicoli
Mentre i NEV diventano sempre più popolari, aumenta di pari passo anche l’autonomia delle vetture, passando dai circa 500 km ai 1.200 km. Per ogni 100 kg di peso risparmiato, l’autonomia dei NEV può aumentare del 10%-11%, mentre i costi e l’usura della batteria si riducono del 20%. Pertanto, l’alleggerimento dei veicoli è diventato un fattore di innovazione essenziale per le principali case automobilistiche e i produttori di componenti perché migliora l’efficienza del gruppo propulsore e ottimizza l’autonomia del veicolo. Ogni casa automobilistica ha adottato una propria “cura dimagrante” per i veicoli, basata sull’utilizzo di nuovi materiali e tecnologie di lavorazione avanzate.
Toyota, BASF e US Farathane hanno sviluppato congiuntamente telai in resina per realizzare per la prima volta sedili dinamici a norma ISO in grado di abbattere i costi del 20% e i pesi del 30%. Inoltre, l’ultima soluzione di Forvia per i pannelli dello schienale dei sedili, Skin Light Panel, è realizzata in monomateriale poliuretano (PU) scolpito in 3D, con una riduzione del peso che va dal 20% al 30%. Marelli inoltre collabora con Covestro allo sviluppo di una nuova schiuma poliuretanica leggera che riduce del 40% il peso del pannello principale del modulo cockpit.
Oltre alla riduzione del peso dei moduli anteriori e dell’abitacolo, anche il pacco batterie, che rappresenta il 20%-30% del peso dell’intero veicolo, ha svolto negli ultimi anni un ruolo fondamentale per l’alleggerimento delle vetture.
Il modello full electric Cadillac Lyriq di General Motors utilizza PA6/12, PA66 e PP di DuPont, Dow e LyondellBasell. Attraverso l’estrusione, lo stampaggio a iniezione, la schiumatura e l’assemblaggio automatizzato, i materiali vengono trasformati in tubi BEV termoplastici per equipaggiare il sistema di gestione termica. I tubi multistrato non solo offrono un’eccellente resistenza chimica, ma consentono anche una riduzione del peso fino al 60%.
Inoltre, i rivestimenti per gli slot delle batterie in materiale PEEK Ajedium di Solvay riducono il peso del pacco batteria e del motore rispettivamente di 12 kg e 4 kg. Mitsubishi Chemical lavora con i partner allo sviluppo di un involucro per le batterie completamente in composito, riducendo inoltre il numero di componenti da cinque a due. Tutto ciò consente a sua volta di alleggerire il peso dell’involucro della batteria. Anche l’involucro in poliuretano HP-RTM di Wanhua Chemical rappresenta una soluzione innovativa che può ridurre il peso fino al 40%-50%. Le tecnologie di lavorazione come lo stampaggio a iniezione con schiumatura integrata svolgono un ruolo chiave nell’alleggerimento dei NEV, come ad esempio lo stampaggio integrato di Engel per il modulo frontale, il processo di schiumatura fisica di KraussMaffei, il processo di microschiumatura di Haitian International, e così via.
Materiali resistenti alle alte temperature e ignifughi per migliorare la sicurezza
Le case automobilistiche stanno innalzando la tensione dell’impianto elettrico dei NEV da 400 V a 800 V. Secondo la legge di Joule, l’efficienza del motore aumenta in proporzione con la tensione. Come conseguenza si migliora l’autonomia della vettura e si riduce il costo della batteria.
Tuttavia, l’impianto elettrico ad alta tensione comporta un aumento significativo delle temperature d’esercizio del motore e della batteria e richiede quindi una migliore gestione termica, il che significa che i materiali devono essere resistenti alle alte temperature e avere proprietà ignifughe.
I principali produttori chimici, come Solvay e DuPont, hanno lanciato nylon ad alta temperatura, gradi PPS e PEEK, film in poliammide e altri materiali adatti a consentire il funzionamento efficiente ad alta temperatura dei propulsori elettrici.
Il modulo batteria dell’Audi e-tron comprende una parte stampata a iniezione con la PA66 fornita di Ems-Grivory, una resina ignifuga classe V0. Fornitori del calibro di Sabic ed Envalior hanno lanciato polimeri ignifughi per garantire il funzionamento sicuro del motore e del modulo batteria. Tra questi, citiamo il nuovo polimero per estrusione di Sabic, adatto alla produzione di pacchi batteria, mentre i materiali termoplastici di Envalior soddisfano i requisiti del refrigerante isolante che circola nel modulo batteria.
Materiali ad alta conducibilità termica per un’efficiente dissipazione del calore
I veicoli a ricarica ultrarapida sono in grado di completare un ciclo di ricarica nel giro di 5-10 minuti. Secondo i dati di Huawei MI, i modelli basati su piattaforme a ricarica rapida ad alta tensione guadagneranno quote di mercato sempre più consistenti, con la prospettiva di arrivare fino a 5,8 milioni di unità entro il 2026, ovverosia il 50% delle vendite complessive di NEV.
A seguito del lancio delle batterie a ricarica ultrarapida da parte di Catl, Sunwoda, Gotion High-tech, Greater Bay Technology e altri, si va diffondendo l’uso di colonnine con connettori di ricarica ultrarapida dotati di raffreddamento a fluido per fare fronte alle più elevate tensioni, intensità di corrente e potenze. Ciò impone che i connettori di ricarica e i materiali del cavo abbiano un’elevata conduttività termica, resistenza e tenacità.
Per soddisfare questi elevati requisiti, la gomma siliconica termoconduttiva HTE5015-90U fornita da Dow e le resine da colata/sigillanti sono in grado dissipare rapidamente il calore che si sviluppa sul connettore di ricarica. Il poliuretano termoplastico (TPU) Elastollan 1180A10WDM di Basf ottimizza le prestazioni dei cavi di ricarica rapida, rendendoli più flessibili e di facile utilizzo.
Materiali ecologici a basse emissioni per ridurre l’impronta di carbonio
Nell’industria automobilistica, ridurre le emissioni di carbonio è ormai una parola d’ordine. BMW, Volvo, Volkswagen, Mercedes Benz, Great Wall, Geely e altri costruttori hanno annunciato i loro obiettivi e piani d’azione per arrivare alla neutralità carbonica. L’utilizzo di materiali ecologici a basse emissioni, come la plastica di riciclo e le resine bio-based, oltre alla rinuncia all’uso di spray, sono tra le misure più importanti implementate dalle case automobilistiche per ridurre le emissioni di carbonio.
Per quanto riguarda la plastica di riciclo, BMW e Volkswagen stanno gradualmente aumentando la percentuale di materiali di riciclo nei nuovi modelli. Da parte loro, Honda e Toray stanno valutando le potenziali applicazioni del nylon 6 riciclato chimicamente nel settore automobilistico, mentre Magna ha introdotto un monomateriale riciclabile al 100% per la produzione dei cuscini in espanso per i sedili e di parti decorative.
Rispetto ai materiali convenzionali a base fossile, i biopolimeri hanno il potenziale per ridurre il costo delle materie prime e negli ultimi anni vengono preferiti in misura crescente dalle case automobilistiche. Concept car come la EV3 e la EV4 di Kia utilizzano fibre naturali e micelio per ridurre l’impronta di carbonio. Polestar e Röchling sono pronte a lanciare il sistema di raffrescamento costruito con materiali bio-based.
La rinuncia agli spray è anch’esso un modo efficace per ridurre le emissioni di carbonio. Gli interni di Toyota utilizzano la poliammide di BASF applicata senza spray, mentre Honda ha unito le forze con Mitsubishi Chemical per sviluppare un colorante PMMA senza spray che può essere utilizzato per la carrozzeria e gli interni delle auto. Molti esempi dimostrano che le case automobilistiche, i produttori di componenti e i fornitori di materiali stanno collaborando lungo l’intera catena del valore per sviluppare una tabella di marcia sostenibile per le materie plastiche destinate al settore automobilistico.
Le auto a idrogeno scendono in pista
Diverse case automobilistiche sono convinte che l’idrogeno rappresenti uno snodo fondamentale nel percorso verso l’obiettivo strategico della neutralità carbonica. I veicoli a idrogeno possono essere riforniti in soli 4-5 minuti e hanno un’autonomia fino a 500 km.
Il modello BMW iX5 a idrogeno ha completato i test su strada in Europa, mentre la Hyundai Nexo è attualmente la vettura a idrogeno più venduta nel mondo, e la Toyota Crown è dotata di tre serbatoi per l’idrogeno che consentono un’autonomia di ben 820 km.
Quindi, quali materiali potrebbero avere un potenziale nelle applicazioni per i veicoli a idrogeno? Il serbatoio dell’idrogeno è per lo più realizzato in fibra di carbonio. La fibra di carbonio ad alta resistenza di Toray viene utilizzata per le bombole ad alta pressione da 70 MPa. Evonik mette a disposizione l’indurente amminico Vestamin per i sistemi epossidici mentre Ancamine può essere utilizzato per una rapida infiltrazione della fibra, consentendo di ridurre fino al 70% il peso del serbatoio. I rivestimenti dei serbatoi dell’idrogeno richiedono polimeri con forti proprietà barriera all’idrogeno al fine di prevenire perdite, come il RILSAN PA11 di Arkema, che può essere utilizzato per produrre i rivestimenti interni delle bombole ad alta pressione resistenti alle basse temperature e ai fenomeni di blistering causati dall’idrogeno ad alta pressione.
L’era dei veicoli full electric si avvicina
Sono sempre più numerose le case automobilistiche che arricchiscono la propria offerta sia in funzione del prospettato boom dei veicoli completamente elettrici sia per soddisfare la domanda di mobilità di lusso che sta emergendo sul mercato cinese.
Alla fiera China International Import Expo 2023, ben 15 case automobilistiche estere hanno messo i NEV sotto i riflettori. Allo stesso tempo, Mercedes Benz, Jaguar Land Rover, Porsche e altri hanno lanciato veicoli elettrici di fascia alta al prezzo di vendita di oltre un milione di yuan.
Con l’acquisizione di Xpeng Motors da parte di Volkswagen e l’investimento di Stellantis, società madre di Maserati, in Leapmotor, i costruttori esteri hanno ribadito l’importanza che attribuiscono al mercato automobilistico cinese.
Per quanto riguarda il mercato globale, l’Unione Europea vieterà la vendita di veicoli a benzina e diesel nuovi entro il 2035, mentre è ufficialmente entrato in vigore l’accordo di partenariato economico regionale asiatico RCEP (Regional Comprehensive Economic Partnership Agreement) che garantisce l’esenzione dai dazi per le automobili e componenti esportati dalla Cina. Queste politiche offrono grandi opportunità all’industria automobilistica del paese. Con Chery, Great Wall e BYD in testa, le case automobilistiche cinesi stanno aumentando la loro proiezione sui mercati esteri.
Un’ultima tendenza emergente tra le case automobilistiche è la ricerca di innovazioni nell’ambito delle joint venture “inverse” e dell’export tecnologico. In questo scenario, anche i materiali e le tecnologie di lavorazione che promuovono l’integrazione dell’IA, l’alleggerimento e la decarbonizzazione dei NEV dovranno affrontare nuove sfide e cogliere nuove opportunità.
Condividi l'articolo
Scegli su quale Social Network vuoi condividere