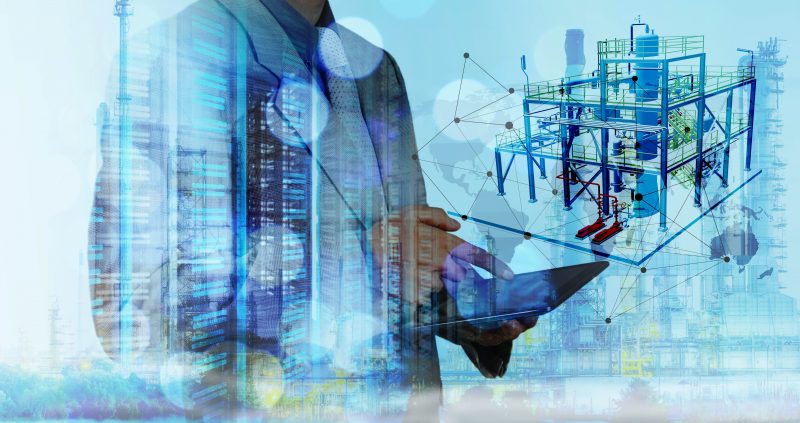
Un esempio di attuazione del processo di digitalizzazione: l'impianto Radici Chimica di Novara. Raccolta, gestione e condivisione dei dati sono finalizzate alla produzione più efficiente e sostenibile dello stabilimento. Superando le criticità, con un occhio alla sicurezza.
RadiciGroup è un’azienda che nasce storicamente nel mondo del tessile, si è sviluppata passando dalle fibre naturali a quelle sintetiche e si è integrata verticalmente sia nella produzione dei polimeri base che nella produzione degli intermedi chimici per la produzione in particolare della poliammide 66.
Il primo schema allegato descrive l’attività, o meglio le aree di business del Gruppo Radici in termini generali.
L’area Specialty Chemicals comprende lo stabilimento Radici Chimica di Novara, fiore all’occhiello della chimica made in RadiciGroup, di cui riportiamo una bella immagine.
Lo stabilimento, di medie dimensioni, dà lavoro a circa 330 addetti e fattura circa 250 milioni di euro. Come si evince dallo schema in fig 3 in questo stabilimento vengono prodotti gli intermedi necessari alla produzione della Poliammide 66 e specificatamente l’acido adipico e l’esametilendiammina.
Combinando questi intermedi con altri di acquisto vengono prodotte anche poliammidi (PA510, PA610, PA612, PA666) con particolari proprietà sia fisiche che chimiche adatte ad impieghi particolari destinati anche altre aree di business del Gruppo:
- High Performance Polymers: produzione di tecnopolimeri per vari settori come automotive, elettrico / elettronico, water management e beni industriali
- Synthetic Fibres: produzione di filati destinati ad abbigliamento, arredamento, tecnico (filo per pneumatici e per airbag).
La situazione precedente all’intervento di digitalizzazione
Il sito produttivo è suddiviso in tre aree ognuna con una sala controllo dove erano posizionati i sistemi di controllo e conduzione degli impianti.
Poiché gli impianti sono stati realizzati in epoche diverse, sono utilizzati sistemi DCS diversi (Schneider e ABB) e PLC Siemens. Per la parte amministrativa è in uso il gestionale JDE. La parte controllo qualità-laboratorio viene gestita dal sistema LIMS Prolab.
Obiettivi del progetto
Già dagli anni ‘90 Radici Chimica ha seguito quelle che erano, e sono ancora, le necessità di un’unità produttiva moderna, efficiente e sostenibile.
Concretamente RadiciGroup ha investito negli anni numerose risorse per l’ammodernamento degli impianti, per lo sviluppo dell’automazione e del controllo, con sistemi elettronici e informatici al passo con lo sviluppo tecnologico.
Negli ultimi anni si è sentita ancor di più la necessità di:
- avere una condivisione dei dati di conduzione degli impianti; cioè dare la possibilità ad alcuni utenti di accedere ai dati di tutti gli impianti senza doversi spostare fra le sale controllo.
- poter estrarre, correlare ed elaborare statisticamente i dati (tecnologia, manutenzione e ingegneria, controllo qualità, sicurezza…).
Criticità connesse all’operazione
Condividere in rete, ancorché interna, i dati dei sistemi di conduzione degli impianti (DCS e PLC) pone inevitabilmente un problema di sicurezza poiché occorre evitare assolutamente interferenze, accidentali o dolose, nei sistemi di controllo degli impianti (temperature, pressioni, livelli, portate eccetera).
Anche la comunicazione tra sistemi DCS, il gestionale JDE e il sistema del Controllo Qualità (LIMS) non è stata esente da difficoltà. Per avere informazione completa è stato necessario aumentare i punti di misura in campo. Inoltre, si è reso necessario implementare procedure e momenti di verifica per esempio fra quelle che possono essere le richieste commerciali (ordine da cliente) e l’impostazione degli assetti produttivi (programmazione produzione).
In impianti chimici come quello di Radici Chimica la catena fra ingresso materia prima ed uscita prodotto è complessa e deve tenere conto degli stoccaggi inziali, dello “hold up” di impianto, dei magazzini o stoccaggi finali.
Questo tipo di impianti a ciclo continuo hanno una “flessibilità” limitata, non permettono grosse variazioni di carico e ancor meno situazioni di “stop and go”.
Elementi del progetto
Per l’implementazione del progetto è stato dato l’incarico ad un’azienda specializzata: Eascon. Eascon ha analizzato in dettaglio la situazione esistente, e, in base alle richieste di RadiciGroup ha elaborato una proposta che è stata approvata e messa in opera. È tuttora in fase di implementazione.
I punti cardine sono i seguenti:
- sviluppo di Tecnologia MES CPP 4.0, che prevede modularità e scalabilità nel tempo;
- upgrade di ingegneria di processo, ingegneria informatica, ingegneria di automazione, per ridurre i tempi operativi di stabilimento;
- acquisizione di competenze normative 14.0.
- contestualmente, si è valutato che un progetto di questo tipo sarebbe potuto rientrare nell’ambito della legge 232/16 che prevede sgravi fiscali per l’innovazione e l’automazione.
Implementazione del processo MES
- Supervisione ed analisi delle prestazioni del processo produttivo
- Tracciatura dei lotti e delle campagne di produzione e condivisione delle informazioni con la logistica
- Programmazione operativa della produzione e verifica dello stato di avanzamento dei programmi di produzione
- Verifica dei requisiti per l’iperammortamento I4.0
Sinteticamente:
- 5 requisiti obbligatori: automazione, interconnessione, interfaccia uomo/macchina, sicurezza.
- ii) 2 su 3 requisiti ulteriori: telecontrollo, adattività, cyberfisici
La road map della digitalizzazione RadiciGroup
Data l’impossibilità di intervenire in blocco su tutto lo stabilimento che avrebbe comportato una sospensione inaccettabile dell’attività produttiva e, come già accennato, un punto qualificante e dirimente è rappresentato dalla possibilità di modulare l’intervento per singoli reparti dello stabilimento e quindi in tempi successivi.
La situazione iniziale vede l’esistenza di numerosi sistemi di controllo NON interconnessi.
Il primo passo è stato quello di rimuovere le macchine ormai obsolete (revamping) predisponendo l’ambiente alla successiva interconnessione. Nel corso del 2018 sono state sostituite 5 macchine (DCS e PLC) e predisposte le nuove realizzazioni (2 sezioni di impianto).
Il passo successivo, nel 2019, è caratterizzato dalla sostituzione di un ulteriore macchina e dalla messa in funzione (interconnessione) del primo embrione del sistema. Il collegamento dei vari server ha permesso lo scambio di informazioni e il popolamento di alcune pagine del MES CCP 4.0
Il programma di attività per il 2020 prevede di estendere la rete di collegamento dati a tutti i reparti/impianti dello stabilimento (Fig 7) e di chiudere il progetto con l’interconnessione completa come rappresentato nella fig. 4 soprariportata.
a cura di Gabriele Modini
Condividi l'articolo
Scegli su quale Social Network vuoi condividere