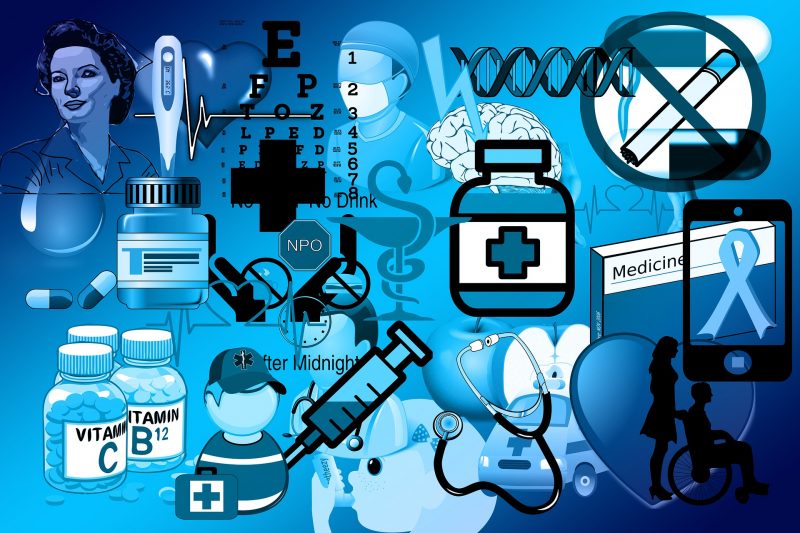
Cellule staminali, dispositivi medici e tessuti sintetici per il comfort del corpo. Questi sono solo alcuni esempi interessanti che mettono in luce l'intenso lavoro e le numerose possibilità che materiali e tecnologie possono ancora dare alla nostra salute e al nostro benessere.
Nel campo della medicina le cellule staminali umane sono la nuova speranza per innumerevoli malattie. Si pensa che in futuro sarà infatti possibile curare, ad esempio, malattie neurodegenerative grazie proprio alle cellule staminali. Dal mondo della ricerca sono tante le innovazioni e gli studi che si focalizzano su di esse. I ricercatori del Franhofer Institut hanno sviluppato un sistema che potremmo definire “tutto in uno” che consente la coltivazione, differenziazione e il congelamento delle cellule staminali in modo rapido, economico e sterile naturalmente. Le cellule prodotte in questo sistema possono essere utilizzate per test di tossicità e per lo sviluppo di nuovi medicinali.
Questa soluzione è stata chiamata LabBag e recentemente è stato presentato il prototipo alla fiera Medica di Duesseldorf.
Gli studi più recenti hanno dimostrato che i modelli cellulari tridimensionali sono quelli che meglio richiamano le condizioni all’interno del corpo umano. La generazione di questi aggregati di cellule avviene principalmente in condizioni sterili sotto forma di soluzioni nutritive. In futuro sarà possibile completare questo processo in modo economico e affidabile. Il progetto LabBag ha coinvolto il Fraunhofer Institute for Biomedical Engineering IBMT, il Fraunhofer Institute for Surface Engineering and Thin Films IST e il Fraunhofer Institute for Process Engineering and Packaging IVV. Il laboratorio in miniatura sviluppato si presente sotto forma di borsa e di plastica. All’interno di questa mini borsa le cellule staminali pluripotenti indotte, ovvero cellule staminali prodotte artificialmente, sono in grado di crescere e di formare degli aggregati tridimensionali in condizioni ambientali sterili.
Fino ad ora il metodo consueto è quello di utilizzare strumenti come pipette e piastre di Petri, con costi elevati e tempi lunghi e con il rischio di contaminazione della coltivazione. Il “laboratorio in busta” sviluppato dagli istituti del Fraunhofer ha lo scopo di ridurre proprio i costi del lavoro e dei materiali necessari. Con LabBag è sufficiente agitare la busta trasparente e nel giro di alcuni secondi si producono centinaia di gocce di soluzione nutritiva che rimangono appese. Queste gocce funzionano come dei bioreattori in cui gli aggregati cellulari si possono formare.
Prima di tutto viene versata la soluzione nella busta. La busta viene poi ruotata una volta e rimessa poi nella sua posizione iniziale. In questa fase le gocce rimangono sospese su dei punti tondi idrofili. Le cellule sprofondano sulla base delle gocce, dove si uniscono tra loro e fondendosi formano un preciso aggregato tridimensionale. La pellicola polimerica della busta è stata rivestita con due diversi rivestimenti. Uno strato base idrofobico assicura che la soluzione nutritiva contenente le proteine si muova lungo questa parete senza rimanerne attaccato. Il secondo strato, invece, consiste in 150 punti tondi idrofili, ognuno con un diametro di 5 millimetri. La soluzione viene letteralmente catturata all’interno di questi punti, con la conseguente formazione di gocce. Per la funzionalizzazione di questa superficie sono stati utilizzati processi al plasma in pressione atmosferica. In questo modo è stato generato del plasma negli spazi di aria tra due elettrodi, applicando tensione alternata. Il plasma viene poi utilizzato per trattare le superfici di diversi materiali.
I modelli cellulari che crescono nel LabBag possono anche essere congelati all’interno della busta, eliminando quindi la tradizionale fase di spostamento in apposito contenitore criogenico. L’attenzione con LabBag è tutta sulle cellulare staminali pluripotenti indotte, perché queste possono essere sviluppate in cellule di qualsiasi parte del corpo, comprese quelle tessutali, e non pongono problemi etici come le cellule staminali embrionali. Nel caso specifico uno degli istituti Fraunhofer si è concentrato, e con risultati positivi, sulla differenziazione di cellule del muscolo cardiaco.
Ogni goccia ha un volume di circa 20 microlitri e le dimensioni del modello cellulare 3D è intorno ai 400 micrometri. Modificando il diamentro del punto tondo sulla superficie della busta, è possibile modificare le dimensioni degli aggregati, così da ottenere l’espansione prescelta della coltura. Allo stato attuale ci sono volute 72 ore per produrre gli aggregati nelle gocce sospese. L’intenzione è anche di aggiungere dei sensori per controllare il processo.
Per la scelta e la messa a punto del materiale, inclusa la parte sigillante, come anche per lo sviluppo della migliore forma e della tecnologia con cui produrre il LabBag, sono stati effettuati diversi test. Questi hanno coinvolto aspetti come la permeabilità, la qualità delle analisi microscopiche, la biocompatibilità e la resistenza alle temperature e ai prodotti chimici. È così che si è arrivati alla scelta di film polimerici, dopo aver tenuto 8 gruppi di polimeri sui 15 analizzati. I requisiti da rispettare sono stati infatti particolarmente difficili. Il materiale doveva infatti essere altamente trasparente e in grado di mantenere la forma, saldabile e impilabile, resistente alla sterilizzazione e al congelamento criogenico. LabBag doveva anche essere maneggevole e facilmente apribile per garantire un rapido e semplice accesso per cambiare le soluzioni nutritive. Per verificare il rispetto di tutti questi requisiti, è stato sviluppato un banco di prova parzialmente automatico per la produzione di queste buste.
Elastomeri piezoelettrici
Un’altra applicazione messa a punto invece da Empa, istituto svizzero per la tecnologia e la scienza dei materiali, può essere utilizzata in diversi settori, compreso quello medicale. L’istituto ha infatti sviluppato un materiale flessibile che genera elettricità quando posto sotto un qualsiasi sforzo. Questo consente di utilizzarlo come sensore integrandolo, ad esempio, nei vestiti oppure impiantandolo nel corpo umano per generare ad esempio la corrente necessaria a un pacemaker.
Questo materiale si caratterizza dunque come film sottile, organico, flessibile che genera elettricità quando teso o compresso. Si tratta di una pellicola in gomma che potrebbe essere inserita in pulsanti di controllo, vestiti, robot e come detto anche impiantato nel nostro corpo. Grazie all’effetto piezoelettrico, questo elastomero è in grado di tradurre i movimenti meccanici in cariche elettriche. Questo è possibile infatti grazie alla polarizzazione interna che cambia quando la pellicola è sottoposta a stress meccanico.
Tuttavia la messa a punto di questi elastomeri con proprietà piezoelettriche non è stata facile. Si tratta di un materiale composito costituito da nanoparticelle polari e un elastomero (silicone nel prototipo). Prima di comporre i due materiali insieme è stato quindi necessario sviluppare correttamente le due componenti. È stato quindi prodotto un film elastico e sottile in cui le molecole polari delle nanoparticelle sono orientate a caso. Per ottenere il materiale piezoelettrico è stata introdotta una polarizzazione interna utilizzando un forte campo elettrico. Il film viene infatti scaldato fino a che è stata superata la temperatura di transizione vetrosa delle nanoparticelle, che sono così passate dallo stato solido vetroso a quello gommoso e viscoso. Sottoposte a queste condizioni, le molecole polari sono orientate dal campo elettrico. Questo orientamento viene poi bloccato in posizione mediante il raffreddamento del materiale a temperatura ambiente.
Una delle applicazioni possibili è proprio quella dell’impianto vicino al cuore, così che il battito cardiaco gli permetta di produrre elettricità per alimentare pacemaker o altri dispositivi impiantati, evitando quindi anche operazioni invasive per cambiare la batteria.
Tutto in uno: tessuto caldo o fresco
Un team di ingegneri della Stanford University in California ha messo a punto un tessuto sintetico che può essere sia caldissimo sia freddissimo a seconda del lato che tocca il corpo.
La parte che riscalda il corpo è stata progettata con del materiale isolante che intrappola al meglio il calore prodotto dal corpo. La messa a punto del lato che invece deve raffreddare il corpo è stata un po’ più laboriosa, poiché solitamente il corpo rilascia calore. È stato quindi messo a punto un materiale che è trasparente alla radiazione infrarossa prodotta dal corpo, con valori di perdita del calore corporeo tra il 40 e il 60%, garantendo così l’uscita del calore.
Il materiale messo a punto è un polietilene spesso 45 micron. Questo viene integrato attraverso delle cavità nanometriche. Questa tipologia di polietilene blocca la luce visibile, così che non si possa vedere attraverso come si è invece abituati, ad esempio, nel caso di tanti imballaggi a base di polietilene. Questo materiale ha struttura sandwich: polietilene in dimensioni nanometriche rivestito con nero di carbonio in grado di assorbire ed emettere l’infrarosso e dall’altra parte uno strato estremamente sottile di rame che assorbe (e rilascia) appena l’infrarosso.
Questa struttura interna tuttavia non è esattamente al centro del tessuto, bensì più vicina a un lato che a un altro. Quando questa struttura interna è rivolta più vicino alla pelle, lo stato di nero di carbonio si trova rivolto verso l’esterno, permettendo così di rilasciare il calore corporeo all’esterno. Se il vestito con questa struttura viene invece indossato con il doppio strato più lontano dalla pelle, lo strato di rame consente di riflettere tutto il calore all’interno, intrappolando così il calore corporeo.
Questo sistema funziona così bene che si è registrata addirittura una differenza di 6,5°C tra le due modalità. Si stima che questa differenza può addirittura ancora esser raddoppiata con ulteriori sviluppi.
Il tutto viene presentato con costi sostenuti, poiché sia il polietilene che il nero di carbonio e il rame sono presenti sul mercato a costi competitivi. Rimane ancora da mettere a punto la durata di questo tipo di soluzione e la sua stabilità in termini di prestazioni anche dopo essere stata sottoposta a lavaggio.
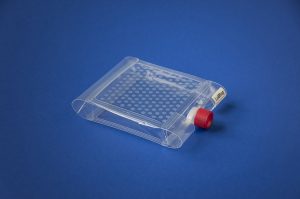
Il LabBag di Fraunhofer Institute è lungo 150 mm, largo 120 mm e spesso 20 mm e il tappo a vite è stampato in 3D
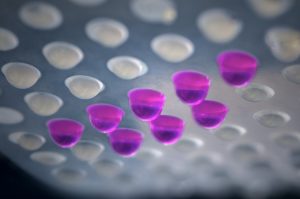
Il LabBag è realizzato in materiale polimerico altamente trasparente, con memoria di forma, saldabile e impilabile, resistente a sterilizzazione e congelamento criogenico, maneggevole e facilmente apribile
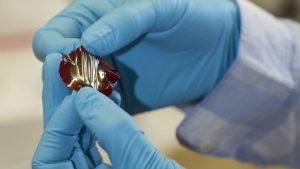
Empa ha sviluppato un materiale in pellicola sottile, organico, flessibile che genera elettricità quando teso o compresso che può essere impiantato nel corpo umano per generare ad esempio la corrente necessaria a un pacemaker
Condividi l'articolo
Scegli su quale Social Network vuoi condividere