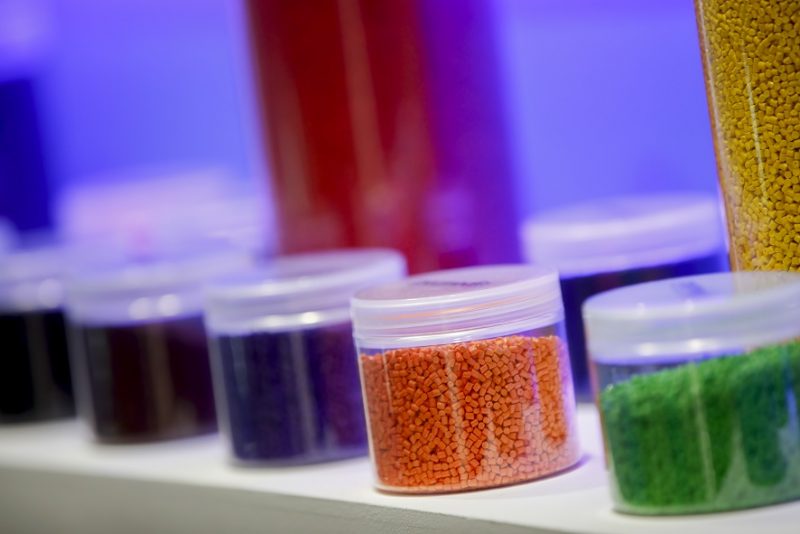
Il masterbatch è una mescola a base di resina con elevata concentrazione di pigmenti ed eventuali additivi. Esso viene aggiunto al materiale polimerico con lo scopo di colorarlo o di conferirgli prestazioni specifiche.
La dispersione delle particelle di pigmento deve risultare adeguata in modo da evitare che le particelle stesse si sciolgano in maniera diversa in fase di lavorazione del polimero.
La gamma di polimeri utilizzabili in forma di masterbatch è molto ampia e comprende resine termoplastiche di base e tecnopolimeri: polietilene, polipropilene, polimeri stirenici, ABS, polimeri acrilici, EVA, PVC.
Classificazione
La gamma di masterbatch esistenti in commercio viene classificata come segue:
- masterbatch neri;
- masterbatch bianchi;
- masterbatch colore o con effetti speciali;
- masterbatch additivi: contengono additivi con determinate funzioni: ritardanti di fiamma, compresi i ritardanti HFFR (halogen free flame retardants), stabilizzanti UV, antiossidanti, scivolanti e anti scivolanti, rinforzanti, lubrificanti eccetera. Possono anche contenere coadiuvanti di processo per rendere il polimero più idoneo in fase di trasformazione.
Masterbatch e coloranti: pigmenti inorganici e organici
I coloranti (pigmenti) usati nei masterbatch possono essere di due tipi:
- pigmenti (coloranti) inorganici: rispetto ai pigmenti organici sono generalmente caratterizzati da una maggior stabilità alla luce e alla temperatura, ma al contempo da una minor brillantezza. I pigmenti organici vengono preferiti nei casi in cui sia richiesta una colorazione particolarmente brillante del manufatto in plastica. I pigmenti inorganici rappresentano comunque ancora la quota di gran lunga più consistente del totale pigmenti utilizzati (circa il 90% in quantità). Numerosissime sono le tipologie di pigmenti inorganici utilizzati: biossido di titanio (classico colorante bianco), carbon black, nero spinello (realizzato con ossidi misti di rame, cromo, ferro), ossido di ferro giallo, giallo nickel rutilo, giallo cadmio, giallo – arancio a base di solfuri di zinco e cadmio, giallo cromo (sali di piombo e cromo), giallo cromo rutilo (ossidi misti di titanio, cromo, wolframio, niobio, antimonio), arancio cadmio, marrone a base di ossidi di ferro cromo e manganese, marrone rutilo a base di ossidi misti di manganese, titanio, cromo e antimonio, marrone a base di ferrito di zinco, rosso cadmio, rosso-arancio a base di sali di cadmio, ossido di ferro rosso, rosso molibdato, verde a base di ossido di cromo, verde cobalto (spinello a base di ossidi misti di cobalto, nickel, titanio, zinco, alluminio), blu cobalto (ossidi misti di cobalto, alluminio e cromo), blu oltremare, e molti altri ancora. Il giallo cadmio ha progressivamente sostituito il giallo cromo per la sua maggior durata nel tempo, per la sua brillantezza, e per la sua minor tossicità. Giallo cadmio, arancio cadmio e rosso cadmio sono particolarmente idonei per la colorazione di manufatti che debbano resistere a processi termo-plastici e chimici a temperature fino a 300°C;
- pigmenti (coloranti) organici, classificabili a loro volta in due sottoclassi:
- pigmenti azoici, caratterizzati dalla presenza del gruppo cromoforo -N=N-, generalmente unito a due nuclei aromatici di uno o più gruppi NH2 o OH: in base al numero di azogruppi contenuti sono classificabili in mono, di, tris, e poli-azocomposti. Forniscono praticamente tutti i colori: blu, giallo, nero, verde. Rappresentano la più vasta classe di coloranti organici usati industrialmente, circa il 70% del totale;
- pigmenti non azoici: ftalocianine (dalla tonalità blu e verde), chinacridonici (rosso bluastro e tono violetto), isoindolidonici, antrachinonici, perilenici, isoindolidonici, ecc;
Masterbatch customizzati
Sempre più spesso si realizzano masterbatch “customizzati”, cioè colorati o additivati in base alle specifiche esigenze del cliente: ad esempio ad effetto metallizzato (contengono polveri metalliche), ceramico, fluorescente (contengono ad esempio solfuro di zinco), opalescente, metamerico (il colore varia a seconda del fascio di luce a cui è esposto il manufatto in plastica).
Modalità di utilizzo del masterbatch
Il masterbatch viene miscelato ai pellet di polimero puro durante le lavorazioni del materiale (ad esempio durante l’estrusione); in questo modo si rende più agevole l’aggiunta degli additivi. Infatti, generalmente gli additivi devono essere presenti nel manufatto finito in percentuali bassissime, per cui senza l’utilizzo del masterbatch si renderebbe necessario aggiungere gli additivi sotto forma di polvere, con conseguenti difficoltà sia nel dosaggio sia nella miscelazione.
L’adeguata dispersione delle particelle di colorante (pigmenti) è un parametro importante per garantire una omogenea colorazione del polimero; essa non si verificherebbe nel caso in cui le particelle non si sciogliessero in maniera omogenea in fase di lavorazione del polimero. Un altro elemento importante è la riproducibilità del colore.
Il mercato dei masterbatch
Si stima che il mercato globale dei masterbatch raggiungerà i 20,53 miliardi di dollari nel 2025, con un tasso di crescita annuale composto (CAGR) del 6,89% nel periodo 2019-2025 (fonte: ResearchAndMarkets.com).
Condividi l'articolo
Scegli su quale Social Network vuoi condividere