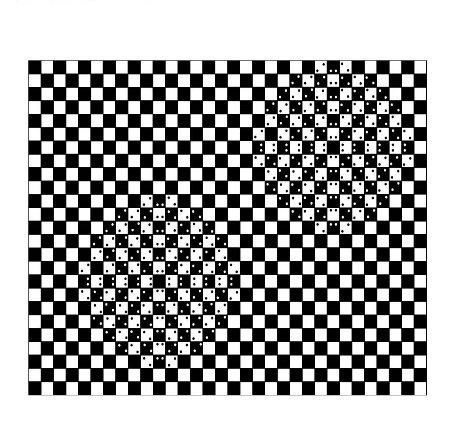
Elementi divisori per ambienti interni realizzati mediante re-bonding di scarti industriali di schiume rigide per isolamento termico. Dal concept ispirato alle illusioni ottiche fino al dimostratore tecnologico del processo di riciclo meccanico.
I poliuretani sono fra i materiali più versatili attualmente disponibili sul mercato. Negli ultimi quarant’anni sono stati impiegati in misura crescente e in una varietà di differenti applicazioni. Uno dei fattori che maggiormente rende il poliuretano così attraente è la sua durabilità, che contribuisce significativamente alla lunga vita utile di molti prodotti realizzati con questo materiale. L’estensione del ciclo di vita dei prodotti e la salvaguardia delle risorse primarie sono importanti considerazioni ambientali che spesso favoriscono la scelta dei poliuretani. A livello mondiale, l’attenzione della comunità tecnico-scientifica si sta concentrando sempre di più sul riciclo del poliuretano a causa dei cambiamenti attualmente in corso su questioni sia normative che ambientali. L’aumento dei costi di smaltimento in discarica e la diminuzione degli spazi destinabili a tal scopo stanno rendendo necessario prendere in considerazione opzioni alternative per la gestione del fine vita dei materiali poliuretanici. L’industria del poliuretano ha identificato tecnologie sfruttabili per il recupero e il riciclo degli scarti poliuretanici sia post consumo che derivanti dai processi di produzione. La maggior parte dei poliuretani viene sottoposta al riciclo meccanico, il quale ha una catena di processo molto semplice che prevede separazioni, triturazioni, macinazioni, addensamenti od altre trasformazioni successive a seconda che si abbia un materiale di partenza omogeneo oppure eterogeneo. Da queste lavorazioni è possibile ottenere dal rifiuto una materia prima seconda che servirà ad altre produzioni. Si parla in questo caso di de-valorizzazione (downcycling) ovvero di riciclo a “circuito aperto”. Lo studio del Cetma, organizzazione di ricerca e tecnologia con sede a Brindisi, è stato indirizzato verso due obiettivi specifici:
- Sviluppare in scala di laboratorio un processo efficace per il riciclo meccanico di scarti industriali di schiume poliuretaniche rigide per isolamento termico;
- Individuare possibili applicazioni di pannelli a base di poliuretano riciclato nel settore arredo.
Progettazione concettuale del divisorio per ambienti interni
Dal punto di vista prettamente tipologico, dopo una serie di studi di mercato per l’individuazione di complementi d’arredo ad uso residenziale o contract, le analisi sono state condotte sull’elemento “divisorio”. Per sviluppare la soluzione si è partiti dalla ricerca sui fenomeni percettivi, ovvero i processi grazie ai quali la nostra mente seleziona le sensazioni per noi importanti, organizzandole in un insieme ordinato e comprensibile, e dalle illusioni ottiche, ovvero inganni a livello psicologico subiti dal nostro apparato visivo e che determinano una scorretta percezione delle forme. La composizione del divisorio è stata ideata come un motivo a scacchiera bianco e nero (Figura 1), al quale per creare movimento ed eterogeneità sono stati aggiunti dettagli non solo decorativi, ma anche sfruttabili dal punto di vista funzionale. Le linee parallele vengono percepite come divergenti, convergenti o curve a seconda della trama adottata. Il risultato è un sistema piano che però illude l’osservatore, rendendosi carico di variazioni e movenze.
Sviluppo sperimentale del processo di riciclo del poliuretano
Gli scarti industriali di partenza sono schiume poliuretaniche rigide per isolamento termico. Si tratta in particolare di sfridi di taglio a bassa densità (35÷50 kg/m3) derivanti dal processo produttivo di un’azienda pugliese che realizza allestimenti coibentanti per veicoli stradali adibiti al trasporto refrigerato di beni deperibili (Figura 2). Tali scarti non sono attualmente interessati da alcuna forma di riciclo, ma interamente destinati allo smaltimento in discarica oppure al recupero come combustibile o come altro mezzo per produrre energia.
Il processo di riciclo sviluppato trae spunto dalla ben nota tecnologia denominata re-bonding, largamente impiegata per il riciclo di schiume poliuretaniche flessibili. Nel corso del presente studio è stato sviluppato un processo analogo che impiega scarti di schiume poliuretaniche rigide ed è quindi volto alla realizzazione di lastre o pannelli rigidi e compatti, aventi densità di diverse volte superiore – dell’ordine di un fattore dieci – rispetto al materiale di partenza. Rispetto alle schiume flessibili, il re-bonding di schiume rigide sembra essere meno comune nel panorama industriale attuale, probabilmente perché occorre ancora sviluppare una efficace filiera <Produttore (degli scarti) → Trasformatore → Utilizzatore>. Il processo di riciclo sviluppato consiste di tre fasi principali:
- Macinazione meccanica degli scarti;
- Miscelazione degli scarti con un opportuno legante (Figura 3a-b);
- Stampaggio a compressione del composto scarti/legante (Figura 3c-e).
Validazione del materiale riciclato
Il semilavorato prodotto col processo di riciclo del poliuretano, come anticipato, potrebbe avere potenziali applicazioni nel settore dell’arredamento, quali allestimenti oppure elementi divisori, piani di lavoro e mensole, eventualmente previo rivestimento con pelli estetiche e/o di rinforzo. In tal senso, il pannello sviluppato potrebbe essere impiegato in alternativa ai tradizionali pannelli di fibra di legno. Si è dunque stabilito di far riferimento alle normative relative a questa tipologia di prodotto per fissare i requisiti ed i metodi di prova rispetto ai quali svolgere la validazione del materiale da riciclo costituente il pannello stesso.
In accordo con la norma UNI EN 316 i pannelli di fibra di legno possono essere classificati secondo diversi criteri, per esempio secondo il processo produttivo, la densità, le condizioni di utilizzo o la finalità d’uso. In particolare, compatibilmente con l’intervallo di densità sperimentato e l’applicazione ipotizzata, si è fatto riferimento ai requisiti specifici per pannelli teneri (230÷400 kg/m3) per uso generale, cioè non portante, in ambiente interno secco (20°C, 65% R.H.). Tutti i test sperimentali sono stati svolti presso Cetma secondo i metodi di prova indicati. I risultati ottenuti sono rappresentati graficamente in Figura 4 ed in Figura 5. Per ciascuna proprietà, è riportato l’andamento in funzione della densità del pannello e del contenuto di legante. In tratteggio viene indicato il requisito specifico relativo ai pannelli teneri per uso generale in ambiente secco. Laddove assente, è stato considerato il requisito relativo ad una categoria di ordine superiore.
Dall’analisi dei risultati ottenuti è possibile estrarre le seguenti considerazioni generali:
- Tutte le grandezze misurate, come atteso, aumentano sensibilmente all’aumentare della densità – ovvero le proprietà meccaniche migliorano e la conducibilità termica peggiora – ma mostrano generalmente una dipendenza meno significativa dal contenuto di legante, il quale potrebbe quindi essere minimizzato al 5% in peso previa ottimizzazione del processo di macinazione degli scarti in termini di granulometria risultante;
- La maggior parte delle configurazioni sperimentate, in termini di densità e contenuto di legante, soddisfano i requisiti prestazionali attesi per la categoria di riferimento, cioè quella dei pannelli teneri per uso generale in ambiente secco, e inoltre in molti casi vengono soddisfatti anche i requisiti relativi a categorie di ordine superiore in termini di densità (pannelli semiduri, 400÷900 kg/m3) o di finalità d’uso (uso portante).
Realizzazione del dimostratore
Il dimostratore finale consiste in un divisorio realizzato mediante no. 25 pannelli a base quadrata di PU riciclato. L’obiettivo esperenziale perseguito è stato quello di produrre un gioco di alterazioni visive variabili a seconda della posizione dell’osservatore. Gli elementi possono essere installati a muro per ricoprire eventuali superfici o a soffitto creando sospensioni verticali fino a pavimento. Assieme al motivo a scacchiera, sono stati ricavati dei pioli che contribuiscono al potenziamento dell’effetto illusorio, oltre che alla funzione di ancoraggio. I pannelli hanno uno spessore di 13 mm, una densità nominale pari a 288 kg/m3 e un contenuto di legante (pre-polimero MDI) del 10% (tipologia M10). Al fine di ottenere il desiderato effetto ottico “a scacchiera”, no. 12 pannelli sono stati realizzati in tonalità chiara e no. 13 in tonalità scura. Gli scarti macinati di partenza (schiuma rigida di PU con densità 35 kg/m3) sono di colore grigio, per cui la produzione dei pannelli chiari non ha richiesto alcun intervento correttivo della formulazione. Per i pannelli scuri, invece, è stato addizionato un opportuno colorante nero al composto scarti/legante.
Successivamente i pannelli sono stati profilati in formato 200×200 mm mediante lavorazione a controllo numerico. Sono stati realizzati, inoltre, i fori per il fissaggio dei morsetti di sostegno – no. 4 per ogni pannello in corrispondenza degli angoli – e i ritagli quadrati laddove previsti – no. 2 lungo il lato oppure lungo la diagonale. I pannelli, infine, sono stati rivestiti su entrambe le facce da uno strato protettivo trasparente per ridurre la polverosità superficiale caratteristica del materiale riciclato costituente. Questa operazione è stata eseguita mediante immersione in una soluzione diluita di colla vinilica la quale, una volta asciugata, ha formato sulla superficie una pellicola sottile di consistenza gommosa.
Lo studio sperimentale svolto dal Cetma su scala di laboratorio ha dimostrato la fattibilità tecnica del processo di re-bonding di schiume poliuretaniche rigide e validato il materiale da riciclo risultante in conformità agli standard relativi ad un prodotto potenzialmente concorrente.
Quanto descritto nel presente articolo è un risultato del progetto di ricerca Maind (Materiali eco-innovativi e tecnologie avanzate per l’industria manifatturiera e delle costruzioni), finanziato dal Miur nell’ambito del programma P.O.N. “Ricerca e Competitività” 2007-2013.
a cura di Ubaldo Spina, Senior Business Development Manager Design & SMEs - Andrea Tinti, Senior Researcher, Polymer and Composite Specialist
Condividi l'articolo
Scegli su quale Social Network vuoi condividere