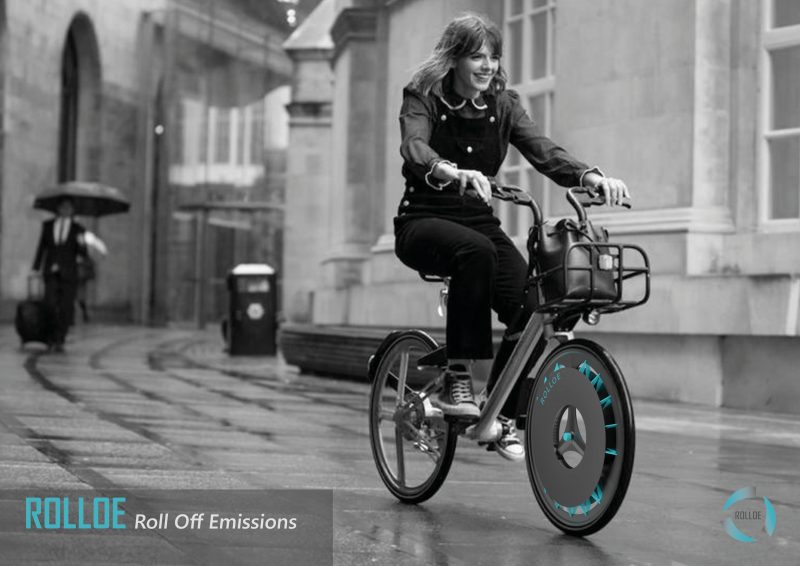
Sport, stampa 3D e materie plastiche. Questa combinazione sta portando sul mercato diversi prodotti che promettono di rivoluzionare il modo in cui si pensa a una qualsiasi attrezzatura sportiva. Calzature, caschi, biciclette sono alcuni esempi di quanto si stia cercando di sviluppare prodotti sempre più sicuri e sempre più su misura, questa ultima ragione per cui la stampa 3D ha molto da offrire. In alcuni casi, tuttavia non è solo la performance o la sicurezza dell’atleta che conta e c’è chi sta già lavorando a prodotti che contribuiscono a migliorare la nostra vita anche su altri fronti.
Una bicicletta realmente “sostenibile”
L’edizione 2020 della competizione Design Innovation in Plastics ha permesso di dare risalto a un progetto dedicato alla vita in città, a cui è stato assegnato il primo premio, che ha il pregio di offrire diversi vantaggi in un’unica soluzione. “Rolloe – Roll off emissions” è un meccanismo applicabile alla ruota anteriore delle biciclette che permette di purificare l’aria contaminata dagli inquinanti tipici delle grandi città, come le polveri sottili. Kristen Tapping, una laurenda della London South Bank University, ha infatti unito la scelta di molti a Londra di andare al lavoro in bicicletta, abitudine favorevole all’ambiente e al fisico del ciclista stesso, a una soluzione che nel contempo permette di pulire l’aria inquinata della città. Un meccanismo adattabile al telaio delle biciclette standard e che per funzionare richiede solo la normale pedalata del ciclista. Per avere rilievo deve esserci un certo numero di ciclisti in giro per la città, ma sembra questo non sia un problema, poiché a Londra vigono regole che invitano i pendolari a utilizzare la bicicletta. La commissione di giudici della competizione ha dunque ritenuto che opportunamente sostenuto e con ulteriori sviluppi, questo progetto potrebbe avere delle buone prospettive commerciali sul mercato.
Secondo la Federazione Europea dei Ciclisti, una bici media emette nel corso della sua vita solo 21 grammi di CO2 per ogni chilometro percorso. Questa quantità comprende 5 g per il processo di produzione e la manutenzione, 16 g per le calorie bruciate dal ciclista. Un veicolo a motore, invece, rilascia 271 g di CO2 a passeggero per chilometro.
Il meccanismo Rolloe utilizza una serie di filtri che intrappolano le emissioni nocive prima di rilasciare l’aria ormai ripulita. Per la realizzazione di questo sistema è stata scelta la stampa 3D. La ruota Rolloe misura 600 x 600 x 60 mm e pesa solo 1,050 kg. Il meccanismo comprende due cerchi con alette in ABS e una ruota centrale in poliammide, che possono essere stampati con produzione additiva o con stampaggio a iniezione. L’ABS è resistente ad abrasione meccanica, ai graffi, a calore e ai solventi, oltre a conferire un aspetto omogeneo alla struttura. La poliammide, invece, garantisce estrema resistenza all’usura e alle sollecitazioni.
Tannus Airless, messo a punto dalla società Tannus, è invece il copertone scelto per questo meccanismo. Si tratta di una gomma piena realizzata con una schiuma polimerica a microcelle chiuse, che garantisce prestazioni e peso paragonabili a quelle degli pneumatici tradizionali utilizzati nelle biciclette.
L’assemblaggio corretto di Rolloe permette di convogliare l’aria all’interno attraverso l’apertura cilindrica interna al cerchio, dove sono alloggiati tre diversi tipi di filtro. L’aria purificata viene poi espulsa attraverso le alette esterne. Il tutto avviene a un ritmo di 0,665 m3 a chilometro.
Il primo filtro è una spugna vegetale in luffa che trattiene le particelle di grandi dimensioni, lavabile e riutilizzabile. Segue il filtro HEPA (High Efficiency Particulate Air Filter) che trattiene il polline e le particelle come il PM 2.5, incluse le polveri rilasciate dai freni e dagli pneumatici e alcuni altri elementi emessi dai veicoli. Questo filtro è composto infatti da foglietti filtranti di microfibre assemblati in più strati che bloccano le particelle solide inquinanti. Infine, il terzo filtro installato è a carbone attivo per intrappolare le molecole di gas, utile quindi per bloccare i composti organici volatili e gli odori. Allo stato dell’attuale prototipo, affinché i filtri siano efficaci, è necessario cambiarli una volta a settimana o comunque ogni 250 km.
Kristen Tapping ha in previsione di mettere a punto anche il prototipo per la ruota posteriore e passare poi alla versione definitiva sempre con la stampa 3D, rendendo le biciclette un mezzo ancor più potente per purificare l’aria inquinata delle nostre città. L’intenzione sarebbe di arrivare alla commercializzazione di questi meccanismi e alla messa in opera di sistemi di raccolta e lavaggio dei filtri, che così risulterebbero riutilizzabili più volte. Si prevede infatti che nella sola Londra con il 10% di penetrazione del mercato con l’installazione della sola ruota anteriore, sarebbe possibile filtrare circa 266.865 m3 di aria in un solo giorno.
Casco per hockey, su misura
La tecnologia Digital Light Synthesis (DLS) di Carbon, ha sviluppato insieme all’azienda CCM Hockey, nota produttrice di attrezzature per hockey, un casco che grazie al suo rivestimento interno assicura massima protezione ai giocatori ed elevato comfort. Il sistema messo a punto con CCM Hockey per questi caschi è stato denominato Super Tacks X con Nest Tech, ove Nest sta per Next Evolution Sense Technology. Questo acronimo richiama proprio le prestazioni che il rivestimento interno con struttura in lattice stampato con tecnologia DLS di Carbon assicura, ovvero elevate traspirabilità, comfort e protezione. Questo casco viene realizzato su misura per l’atleta e grazie alla sua struttura garantisce un controllo preciso dell’assorbimento e della dissipazione dell’energia da impatto. Affinché il Super Tacks X potesse rispondere pienamente a tutte queste esigenze, Carbon ha sviluppato la struttura interna reticolare con il suo software Design Engine, che permette di generare automaticamente la struttura, ottimizzandola secondo i parametri di prestazione e peso. L’assorbimento e la dissipazione dell’energia da impatto sono possibili grazie all’allineamento dei montanti di smorzamento interni contro le direzioni dell’impatto subito. Vi sono oltre 130mila montanti realizzati ognuno secondo la loro posizione sulla testa e nel casco, ciascuno quindi con uno spessore diverso e di conseguenza con un grado di rigidità diverso, così da garantire sempre il migliore assorbimento e la massima dissipazione dell’energia da impatto.
La struttura a reticolo, inoltre, assicura un comfort notevole, consentendo all’aria di circolare.
Il casco Super Tacks X è già stato testato sul campo da tre giocatori durante il campionato 2020 della National Hockey League (NHL) e sarebbe intenzione della società CCM Hockey di renderli disponibili a tutti i professionisti per la stagione 2021 e di lanciare sul mercato nella primavera del prossimo anno una versione per i non professionisti con alcune delle soluzioni tecnologiche adottate nel casco professionale, utilizzando sempre la stampa 3D per la parte interna.
Dal piede alla scarpa
Il settore delle calzature sportive è un altro ambito che da alcuni anni mostra particolare interesse per la stampa 3D. Vi sono infatti diversi esempi di aggiornamenti tecnologici della scarpa sportiva, in termini di prestazioni, materiali, processi. Tra questi uno recente viene da HP 3D Printing Solutions, che ha messo alla prova una scarpa da corsa realizzata “su misura” con alcune parti stampate mediante produzione additiva. Il prototipo è stato testato su una corsa di 5 km. Si caratterizza per avere intersuola e soletta personalizzate e stampate in 3D con la tecnologia HP Multi Jet Fusion (MJF). La scarpa pesa meno di 200 grammi, ha una tomaia leggera e assicura un elevato grado di ritorno di energia e di ammortizzazione. L’intenzione di HP è di personalizzare le scarpe per gli sportivi e renderle a prezzi accessibili, grazie a tecnologie come la FitStation Powered by HP, in grado di scansionare il piede dell’atleta, analizzarne l’andatura e creare un modello 3D digitale del piede. Questo sistema permette di inviare poi a una stampante 3D della HP come la Multi Jet Fusion serie 5200 o la Jet Fusion serie 4200 un modello digitale perfetto per creare una soletta che può essere utilizzata anche su diverse scarpe.
Tra i materiali utilizzati per questo tipo di stampe vi è il poliuretano termoplastico Ultrasint con il grado TPU01 di Basf. Si tratta di una polvere multiuso ideale proprio per la produzione di parti che devono garantire assorbimento dell’energia da impatto, ritorno di energia ed elevata elasticità. Questo grado è stato messo a punto da Basf 3D Printing Company proprio per la serie 5200 delle stampanti HP Multi Jet Fusion. Questo materiale offre al contempo robustezza, flessibilità e durata delle prestazioni, oltre a notevole qualità della superficie, un alto livello dei dettagli e la possibilità di realizzare finiture e lisciatura. Ultrasint TPU01 risulta di facile lavorazione, ha una elevata stabilità di processo e permette tempi di produzione rapidi che si traducono in una elevata produttività.
Un altro materiale che viene utilizzato da HP per la stampa di calzature sportive è il poliuretano termoplastico Estane 3D TPU M95A di Lubrizol, anch’esso studiato appositamente per la produzione additiva e nel caso specifico scelto da HP per la sua serie Jet Fusion 4200. Questa combinazione potrebbe permettere la produzione in serie di calzature.
a cura di Valeria Mazzucato
Condividi l'articolo
Scegli su quale Social Network vuoi condividere