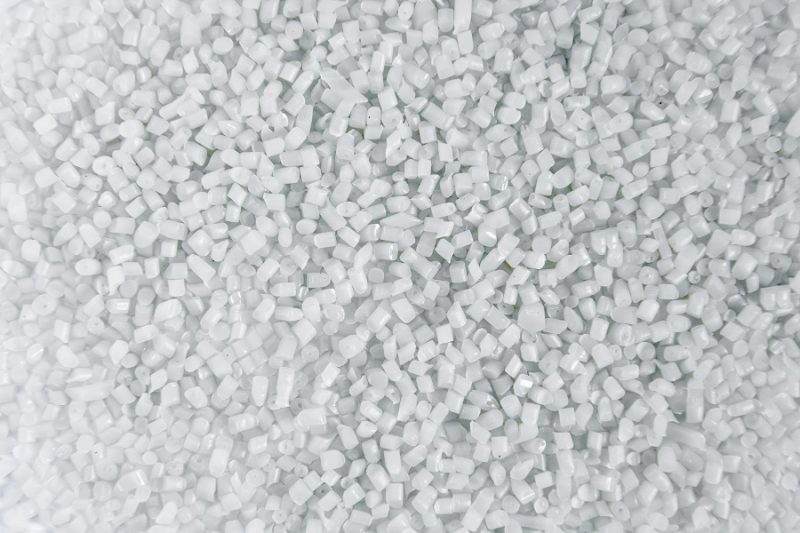
Gli additivi per materie plastiche sono composti che vengono aggiunti alla massa polimerica per migliorarne caratteristiche e prestazioni. Numerosissime sono le tipologie di additivi esistenti in commercio; nel dimensionamento del mercato si tratta di definire che cosa si comprende e che cosa si esclude.
Additivi per materie plastiche: a cosa servono
- migliorare, modificandole, le caratteristiche del manufatto;
- migliorare la lavorabilità in fase di trasformazione del compound polimerico in manufatto finito; in questo secondo caso vengono più propriamente definiti “coadiuvanti di processo” (processing aids).
Tipologie di additivi per materie plastiche
Le principali classi di additivi per materie plastiche sono le seguenti:
- agenti antistatici: questi possono essere aggiunti come parte di un mix di additivi in fase di produzione della plastica (in tal caso vengono chiamati agenti antistatici interni), oppure applicati direttamente sulla superficie del manufatto (antistatici esterni). Gli agenti antistatici possono essere cationici, anionici, non ionici o anfoteri; a tutt’oggi i più usati sono quelli non ionici: esteri di acidi grassi, alchilammine etossilate, dietanolammidi, alcoli etossilati. Gli impieghi più consistenti sono nella strumentazione elettronica e in film speciali per imballaggio
- agenti espandenti (noti come CBAs Chemical blowing agents): sono composti chimici che liberano gas per decomposizione termica o reazione chimica. Comprendono prodotti chimici, quali: isocianato e acqua per schiume poliuretaniche, azo-derivati quali l’azo-di-carbonammide, l’idrazina e altri composti a base azoto per materiali termoplastici e schiume elastomeriche, il bicarbonato di sodio anch’esso usato per schiume termoplastiche, ecc.
- ritardanti di fiamma: vengono aggiunti per ridurre l’infiammabilità dei polimeri, contrastandone le proprietà di accensione, la propagazione della fiamma e l’emissione di fumi tossici. Sono suddivisi in:
- composti bromurati (halogenated flame retardants): la Direttiva UE sulla limitazione delle sostanze pericolose (RoHS) ha proibito dal 1° luglio 2006 l’impiego, nei nuovi componenti elettrici ed elettronici, di alcuni tipi di ritardanti di fiamma: tra quelli messi al bando comparivano il PPB (poli-bifenil bromurati) utilizzati nello stampaggio di materie plastiche, e il PBDE (eteri di difenil polibromurato) generalmente utilizzato nello stampaggio a iniezione delle materie plastiche.
- composti halogen free: il più usato è l’allumina tri – idrata. Altri composti usati sono i composti inorganici (es. ossido di magnesio e borati di zinco), i composti a base fosforo (fosfati organici e inorganici, fosfonati e fosfoniti, fosforo rosso), i prodotti a base azoto (i più usati sono i derivati della melammina, quali cianurati, polifosfati, melem, melam, melon, spesso usati in miscela con prodotti a base fosforo), ecc;
- plastificanti: vengono aggiunti al polimero allo scopo di rendere flessibile il manufatto finale, modificando la molecola interna del polimero. Su un consumo totale mondiale di circa 7.500.000 tonnellate nel 2012 circa il 90% dei plastificanti viene impiegato nel PVC; l’impiego più consistente è in edilizia (pavimentazioni e ricopertura di pareti), seguito dalle guaine di cavi e conduttori isolati. Sono suddivisi in:
- gli ftalati, che, a loro volta, possono essere ad alto peso molecolare (HMW) quali il DINP (di – isononilftalato), il DIDP (iso – dodecilftalato) o il DPHP (di – 2 – propil ottilftalato), oppure a basso peso molecolare (LMW);
- altri prodotti chimici: sebacati, citrati, adipati, azelati, di-benzoati, esteri del poliolo, fosfati, alchilfosfonati aromatici, isobutirrati, esteri acidi del cicloesano, o prodotti di origine vegetale (es. oli vegetali modificati).
- antiossidanti: hanno il ruolo di inibire il processo ossidativo a cui gran parte dei polimeri vanno soggetti o in fase di processo oppure durante il ciclo di vita utile del manufatto, per effetto di luce e calore, stress meccanico, reazione con impurità presenti, ecc.
- stabilizzanti al calore: Possono agire sia prevenendo (almeno in parte) il processo di deidro – clorurazione per reazione con gli atomi di cloro (stabilizzanti al calore primari), sia ritardando la velocità del processo di degradazione, espellendo l’HCl, catalizzatore del processo di degradazione (stabilizzanti al calore secondari). Le più comuni classi di stabilizzanti al calore tradizionalmente usate sono stati i sali di piombo, altri sali metallici e i composti organo – stannici (mercaptidi)
- stabilizzanti alla luce: proteggono nel lungo periodo il manufatto in plastica dalla degradazione derivante dall’azione della luce. Possono funzionare in vari modi:
- come assorbitori di raggi UV: fungono da assorbitori dei raggi UV prima che questi possano danneggiare il polimero, trasformandoli in “quanti di energia” inoffensivi. I più comunemente usati sono idrossibenzofenoni e idrossibenzotriazoli;
- come spegnitori (quenchers) dei punti eccitati dalla luce che altrimenti farebbero da promotori della degradazione del polimero: i più usati sono i composti organici del nickel. Sono utilizzati soprattutto nei film per agricoltura e spesso lavorano in sinergia con gli assorbitori UV;
- come “radical scavengers” (letteralmente “ripulitori di radicali”):
- come schermatori della luce (light screners): sono generalmente pigmenti opachi, non considerati come prodotti chimici “specialty”.
- lubrificanti: hanno la funzione di evitare azioni abrasive sulla massa termoplastica fusa che debba passare attraverso orifizi, ugelli o angoli stretti in fase di lavorazione del polimero. Possono essere di due tipi:
- catalizzatori perossidici: la caratteristica dei perossidi di decomporsi in radicali liberi li rende idonei ad essere utilizzati nell’industria delle materie plastiche
- altri vari: comprendono: disattivatori di metalli, biostabilizzanti, agenti nucleanti, agenti antinebbia (antifogging agents), agenti anti-opacità (optical brighteners), agenti scivolanti, anti-scivolanti e antiaderenti, agenti di accoppiamento (coupling agents).
Il mercato degli additivi per materie plastiche
Il mercato degli additivi per materie plastiche è stato valutato a 28,53 miliardi di dollari nel 2020 e si prevede che raggiungerà i 38,77 miliardi di dollari entro il 2026 crescendo a un CAGR del 5,24%.
Condividi l'articolo
Scegli su quale Social Network vuoi condividere