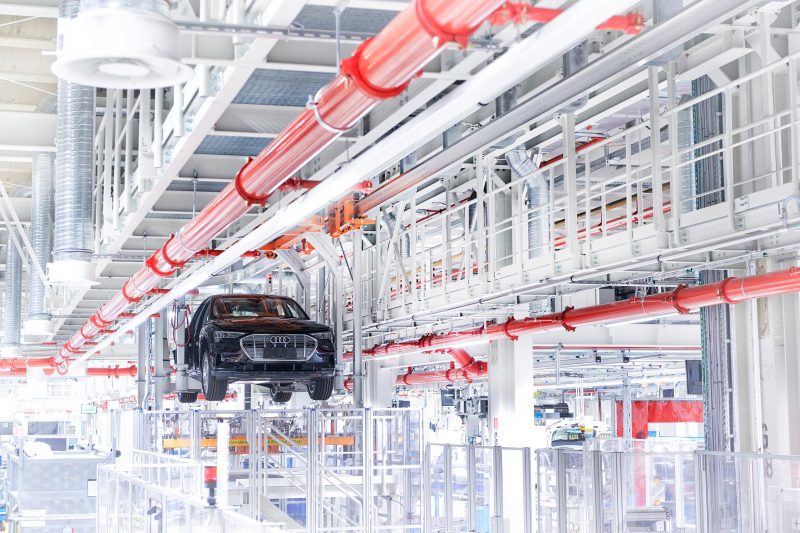
Progetto pilota di Audi con il Karlsruhe Institute for Technology: il riciclo chimico consente il recupero della plastica mista. Il materiale esausto viene trasformato in olio di pirolisi che può essere utilizzato per realizzare nuovi componenti. Sistemi circolari intelligenti all’interno della filiera e utilizzo intelligente delle risorse.
Molteplici componenti delle vetture sono realizzati in plastica e devono soddisfare precisi requisiti di sicurezza, resistenza al calore e rigidità strutturale. Sino ad ora, solo i materiali a base di petrolio – nella maggior parte dei casi difficilmente riciclabili – si sono rivelati adatti in ambito automotive. La plastica “pura” può essere smaltita meccanicamente e successivamente riutilizzata, mentre il recupero della plastica “mista” rappresenta una sfida tuttora aperta. Audi e il Karlsruhe Institute for Technology (KIT) lanciano un progetto pilota per il riciclo chimico dei polimeri misti così da introdurre un innovativo ciclo chiuso della plastica.
“Vogliamo creare dei sistemi circolari intelligenti all’interno della nostra filiera e utilizzare le risorse in modo sempre più efficiente”, afferma Marco Philippi, direttore di Audi AG per gli Acquisti. “Il riciclo chimico presenta delle grandi potenzialità in tal senso. Se divenisse possibile produrre i componenti in plastica mediante l’olio di pirolisi piuttosto che il petrolio, la sostenibilità delle vetture si rafforzerebbe nettamente. Nel lungo periodo, i materiali così ottenuti favorirebbero l’ulteriore riciclo dei veicoli giunti a fine vita”.
Il progetto pilota, denominato “Riciclo chimico delle materie plastiche nel mondo automotive”, mira alla creazione di un ciclo chiuso della plastica e si affianca al più comune recupero meccanico. In collaborazione con il Karlsruhe Institute for Technology (KIT), Audi intende testare la percorribilità di questa nuova soluzione, vagliandone la sostenibilità economica e ambientale. Le valutazioni sono affidate al team guidato dal professor Dieter Stapf presso l’Istituto di Chimica Tecnica e dalla dottoressa Rebekka Volk presso l’Istituto per la Produzione Industriale. A tal fine, Audi fornisce componenti in plastica giunti a fine vita come serbatoi del carburante, copricerchi e griglie radiatore, destinati a essere trasformati nell’olio di pirolisi mediante riciclo chimico. Le qualità di questo olio, definito bio-greggio, corrispondono a quelle dei derivati del petrolio e i materiali realizzati mediante olio pirolitico garantiscono le stesse caratteristiche dei componenti originali. In aggiunta, quanto prodotto con il bio-greggio può essere ulteriormente recuperato e riciclato.
I rifiuti di plastica mista
Ad oggi, il riciclo chimico è l’unica soluzione per convertire i rifiuti di “plastica mista”. Un ciclo chiuso che consente di sfruttare un quantitativo inferiore di materie prime, a vantaggio del saldo energetico complessivo. Audi è tra i primi costruttori al mondo a testare questo innovativo metodo di recupero nella produzione di automobili. “Sinora non era possibile riciclare gran parte delle plastiche utilizzate in ambito automotive. Ecco perché, con Audi, stiamo portando avanti un lavoro che definirei pionieristico”, sottolinea il professor Dieter Stapf, Direttore dell’Istituto di Chimica Tecnica del KIT. “Se vogliamo chiudere il ciclo della plastica, dobbiamo sviluppare una strategia non convenzionale”.
Il progetto è condotto dal centro di ricerca Industrial Resource Strategies che il governo dello Stato federato del Baden-Wùrttemberg ha creato presso il KIT e che adotta una visione olistica per ottimizzare Lo sfruttamento delle materie prime. “Il riciclo chimico può essere la soluzione definitiva per il recupero della plastica e, conseguentemente, per il rafforzamento della sostenibilità delle vetture, indipendentemente dal tipo di propulsione”, afferma Christian Kuhne, amministratore delegato del centro di ricerca.
Audi e i fornitori della Casa dei quattro anelli considerano il riciclo chimico un’opportunità. Il Programma Audi C02 si pone l’obiettivo dello sfruttamento razionale ed efficiente delle risorse, riducendo le emissioni all’interno dell’intera filiera produttiva e concentrandosi, come nel caso dei componenti in plastica, sull’ottimizzazione della gestione dei materiali che comportano un maggiore dispendio energetico. Un esempio virtuoso, in tal senso, è il ciclo chiuso dell’alluminio, grazie al quale Audi recupera gli scarti in lega leggera raffinandoli sino a raggiungere il livello qualitativo necessario per la realizzazione di nuovi prodotti, evitando d’immettere in atmosfera circa 150.000 tonnellate di C02 nel solo 2019.
Oltre 100 bottiglie riciclate per i rivestimenti in abitacolo
La Casa dei quattro anelli ha pianificato un graduale aumento del ricorso ai materiali secondari, ottenuti dal riciclo. L’esempio più recente consiste nell’impiego del PET per la realizzazione dei rivestimenti di nuova Audi A3. Il PET è un polimero plastico che può essere separato dagli altri materiali con cui viene combinato. Una caratteristica che ne favorisce il recupero. Nel caso della quarta generazione di Audi A3, sono disponibili tre diversi rivestimenti in tessuto dei sedili, con una percentuale di filato riciclato sino all’89%. Il risultato? Tessuti che, dal punto di vista visivo e tattile, assicurano gli stessi standard qualitativi dei rivestimenti classici.
Dal vuoto a rendere al filato sintetico
In Germania e in molteplici Paesi europei, le bottiglie vuote vengono inserite in apposite macchine automatiche per ricevere in cambio un incentivo sino a 25 centesimi al pezzo. Ma cosa succede successivamente? Le bottiglie usa e getta vengono pressate e compattate al fine di limitarne l’ingombro per il trasporto. Una volta giunte presso gli impianti di riciclo, vengono suddivise in base al colore, alle dimensioni e alla qualità di conservazione.
Separati i materiali estranei, ad esempio i tappi, una specifica macina sminuzza le bottiglie fino a ottenerne “fiocchi” destinati a essere lavati, asciugati e fusi. Creata una massa uniforme, degli ugelli danno vita a filamenti senza soluzione di continuità che, dopo il raffreddamento, vengono sminuzzati. Il granulato così prodotto viene trasformato mediante estrusione in filato che, dopo essere stato avvolto su bobine, è destinato alla produzione dei tessuti.
Rivestimenti dei sedili, moquette e inserti insonorizzanti
Per realizzare i rivestimenti dei sedili di nuova Audi A3 sono necessarie sino a 45 bottiglie in PET da 1,5 litri. A queste si aggiungono ulteriori 62 bottiglie riciclate, destinate alla moquette. La sostenibilità dell’abitacolo della nuova generazione della compatta dei quattro anelli è ulteriormente rimarcata da molteplici componenti prodotti facendo ricorso a materiali residui: ad esempio gli inserti insonorizzanti e di smorzamento delle vibrazioni, i tappetini e le superfici laterali del bagagliaio. Nei prossimi anni, Audi mira ad aumentare sensibilmente l’utilizzo dei materiali riciclati, garantendo ai Clienti la consueta qualità dei prodotti.
Ad oggi, i rivestimenti dei sedili non sono integralmente in materiali riciclati. “La sfida è rappresentata dal tessuto inferiore, legato al materiale superiore mediante un collante. Stiamo lavorando per sostituire quest’ultimo con una soluzione in poliestere riciclabile”, afferma Ute Grönheim, responsabile per lo sviluppo dei materiali tessili di Audi AG. “L’orizzonte è produrre i rivestimenti con riciclati puri, destinati a un ulteriore riutilizzo così da dare vita a un circolo virtuoso. Non siamo lontani da questo obiettivo». In futuro, i rivestimenti tessili di tutte le gamme Audi saranno realizzati in materiali riciclati.
A bordo di nuova Audi A3 vengono adottate diverse tipologie di rivestimenti composti sino all’89% da materiali riciclati. Il tessuto in grigio acciaio, denominato Torsion, può essere impreziosito da cuciture gialle a contrasto. La versione Puls viene offerta nella combinazione cromatica nero-argento con impunture grigio roccia. Successivamente al lancio, debutterà una variante in nero-rosso con cuciture rosse. All’interno delle diverse linee di allestimento, i rivestimenti in tessuto riciclato costituiscono la base dell’offerta e prevedono fianchetti in similpelle.
Condividi l'articolo
Scegli su quale Social Network vuoi condividere